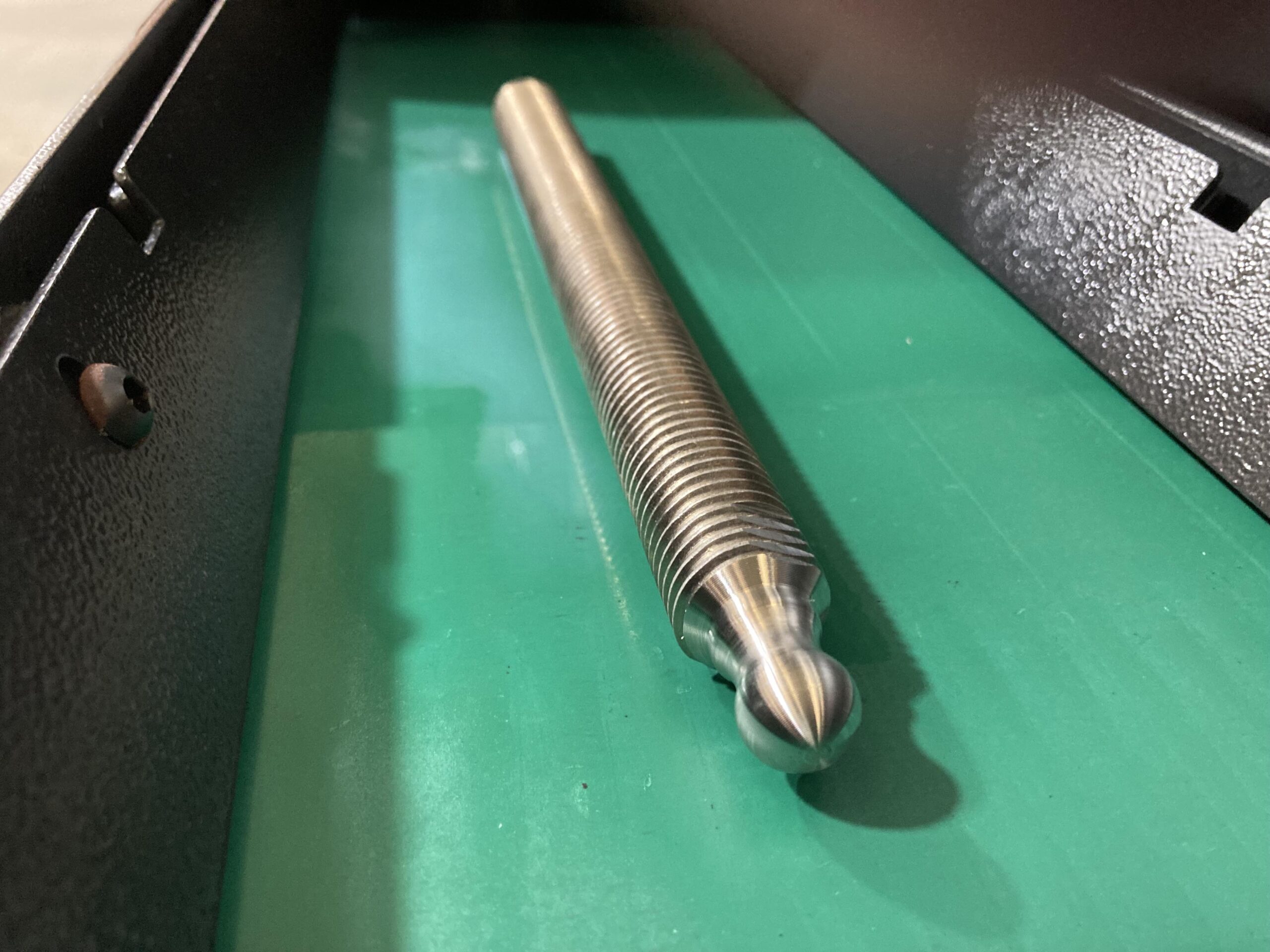
Arnott Handling Equipment has invested in a multi-tasking lathe and bar feeder from Mills CNC to help automate its small-part processing operations. The acquisition by the precision conveyor system manufacturer will also improve productivity and process efficiencies.
The latest investment underscores the company’s commitment to continuous improvement and its business growth strategy that emphasises replacing older equipment and labour-intensive processes with sophisticated, multi-tasking technologies.
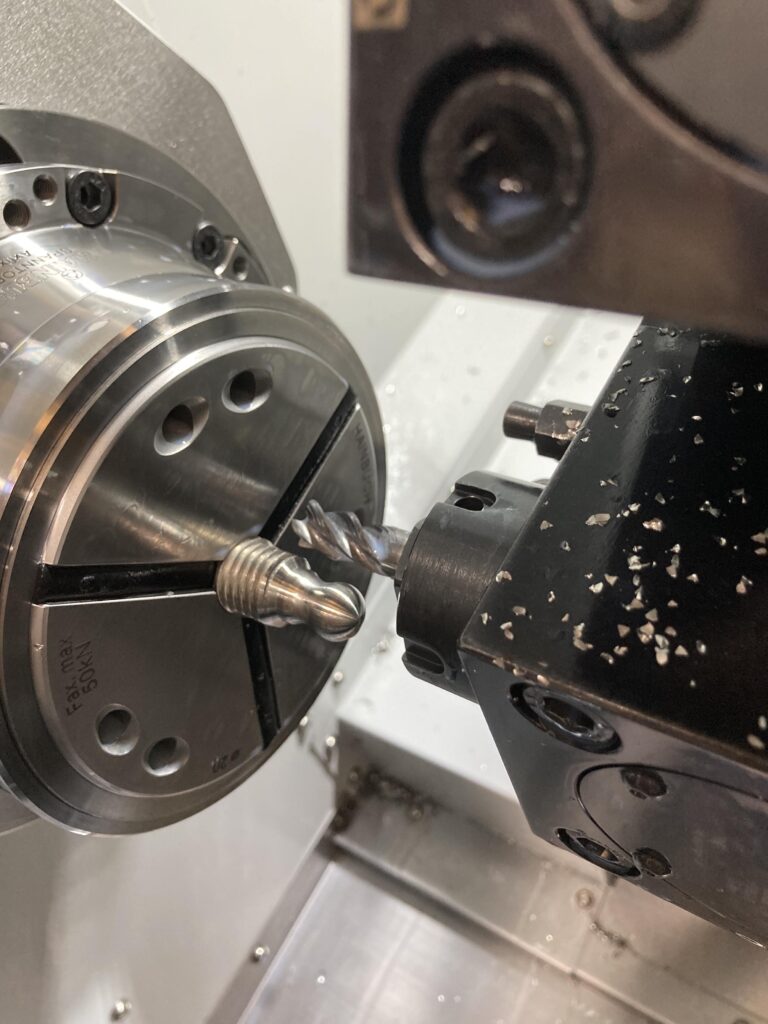
The Lynx 2600SY lathe with a FANUC CNC is a Y-axis sub-spindle variant with a Hydrafeed bar feeder installed at Arnott Handling’s facility in Brixworth. Since its installation, the Lynx 2600SY has machining a diverse range of high-precision, engineered components and accessories for the company’s UK-based conveyor and handling system customers.
Oliver Rippin, Arnott Handling’s Operations Director: “Our customers provide conveyor system solutions to end-users in the retail and e-fulfilment, warehouse and distribution, food, beverage, cosmetics, packaging, pharmaceutical and logistics industries.”
One of the main customers is sister company, Arnott Conveyors Ltd., a manufacturer of bespoke conveyor systems and turnkey solutions for customers.
Nick Howells, Commercial Director: “Sales for our handling and conveyor businesses have been upward. Consequently, we have invested in our people, plant and our processes to meet the increase in demand and achieve sustainable business growth.”
Arnott Handling regularly benchmarks and reviews its KPIs as part of its continuous improvement programme. The monitoring and evaluation process helps identify issues and potential ‘weaknesses’ that could affect future performance and profitability. At the beginning of 2024, the company’s existing machining capacity was under pressure because it won a new contract to supply a large volume of drums for conveyors.
Remembers Oliver Rippin: “The new drum contract brought machining capacity issues to the fore – specifically relating to machining our adjustable feet products.These feet, comprising two separately machined parts, required three different machining operations using two CNC machines to complete each component. The existing process was labour-intensive and required staff to be on hand continuously to perform part loading and unloading. Because the new drum contract would significantly eat into existing capacity and could cause production bottlenecks, we decided to streamline this process by investing in a new multi-axis lathe, with Y-axis and sub-spindle capabilities, to machine both the base and stem components of our adjustable feet.”
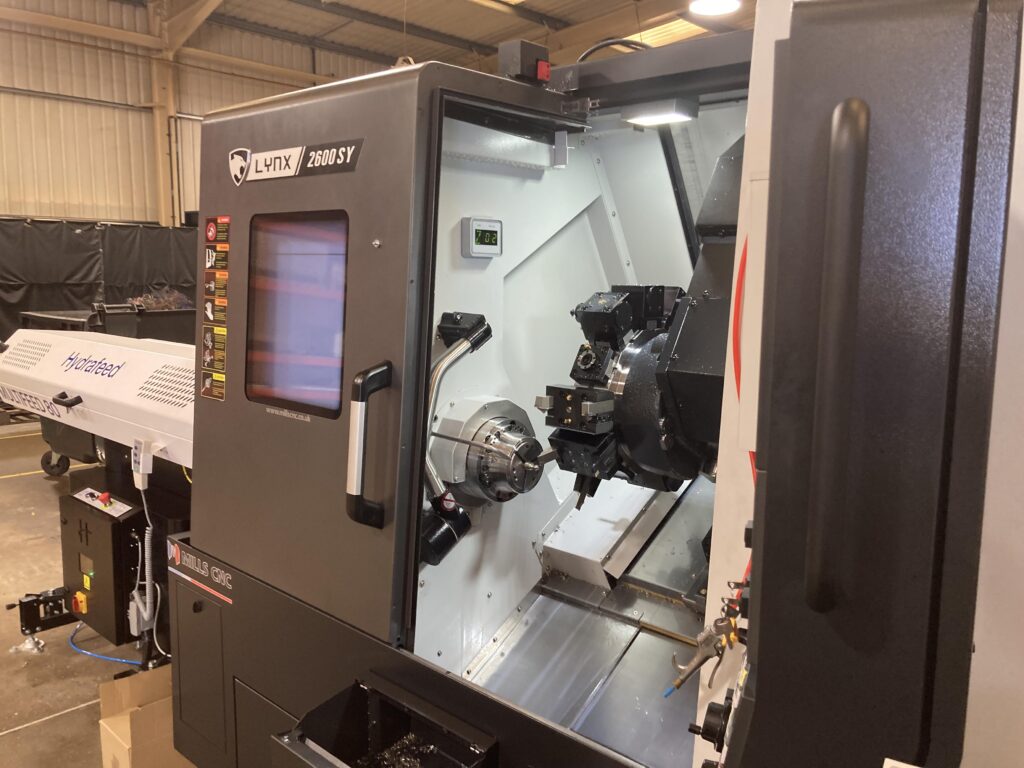
Having previously purchased a DN Solutions’ Puma GT 2600LM box guideway lathe from Mills CNC in 2021, the company was familiar with DN Solutions’.
“It was apparent that the machine’s sub-spindle, driven tooling, and Y-axis capabilities would enable us to machine our adjustable feet components in one set-up, removing the need to transfer parts between different machines.”
Furthermore, integrating a high-performance bar feeder, delivered to Arnott Handling as part of the investment package, would enable the company to create a flexible, high-productivity cell.
The machined materials vary according to the end application and include mild steels, stainless 314 and 316, aluminium, titanium and engineering plastics.
Machine cycle times are short (typically a couple of minutes for the base and stem components), and part tolerances and surface finish requirements can be tight. Since its installation, the Lynx 2600SY hasn’t missed a beat and is meeting its quality and productivity targets as intended.
The Lynx 2600SY features fast 30m/min rapids, a powerful 18.5kW high-torque spindle, and a 12-station servo-driven turret with 5,000rpm tooling capabilities. The Lynx 2600SY’s versatility is delivered, in part, via its integrated 6” chuck sub-spindle (4500rpm) and its +/-52.5mm Y-axis.
Subscribe to the MTDCNC Newsletter
Subscribe to our Newsletter today!
Stay up to date with the latest industry news and events.
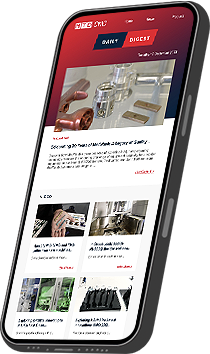