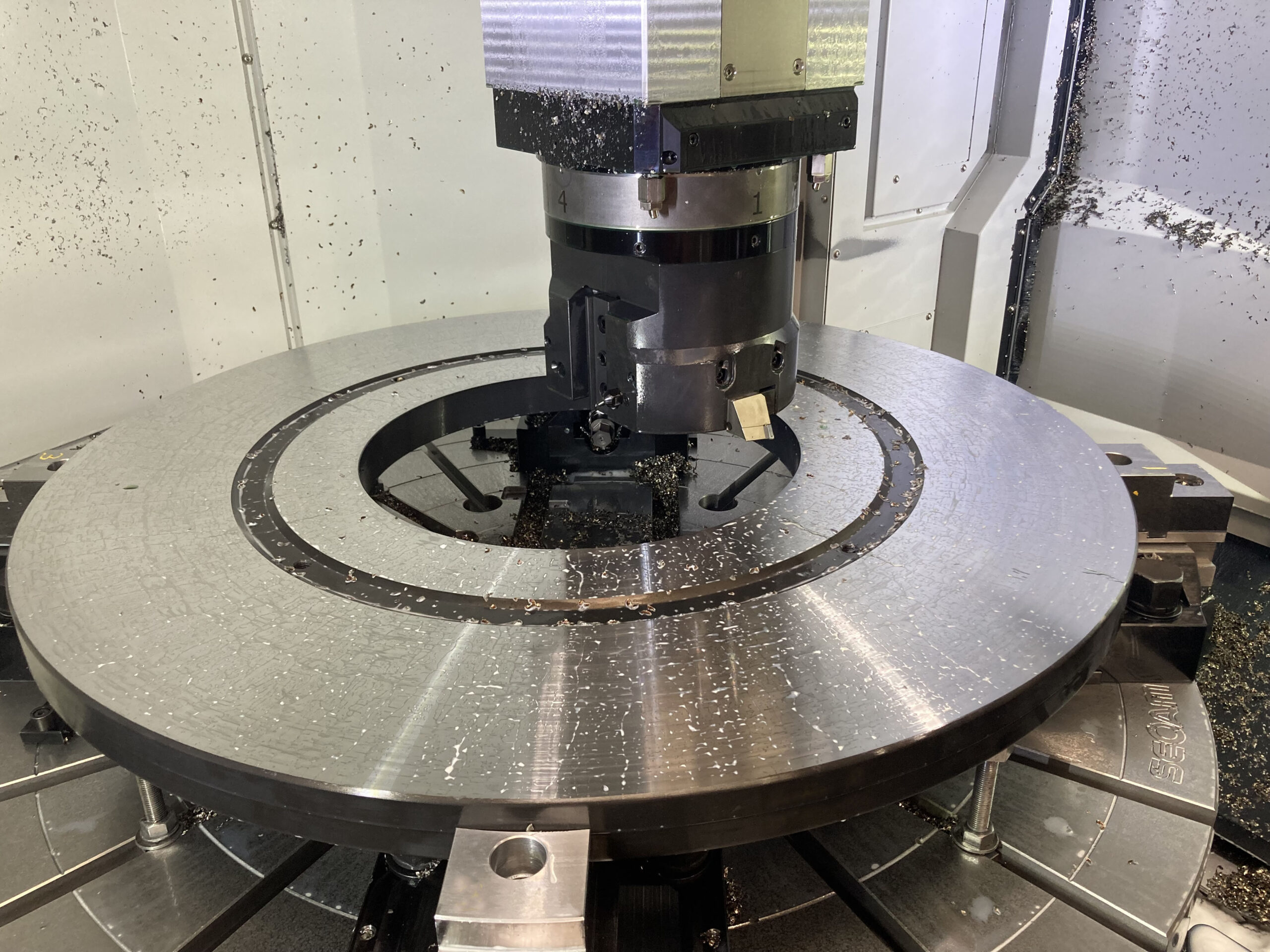
As a roll tooling and equipment design and manufacturing specialist, Bowers & Jones Ltd is increasing its in-house machining capacity and capabilities by investing in a new DN Solutions large-capacity, ram-type vertical turning lathe. The VTR 1216F machine from Mills CNC was acquired to fulfil a new steel mill order from a customer in the US that requires batches of high-precision straightening rings.
Additionally, owing to the machine’s size, power, precision and versatility, the new investment will also help generate new business opportunities and growth in the US and other markets, consolidate its supply chain position with existing steel mill customers, and improve its UK precision subcontract machining operations.
The new VTR 1216F machine is a large-capacity wide-column ram-type vertical turning lathe. It has been installed at the company’s 15,000sq/ft manufacturing facility in Bilston, near Wolverhampton, joining three previously acquired Mills machines supplied over the last four years. The existing machines are a Doosan Puma 5100B lathe installed in 2020, a Doosan DNM 750 II VMC with a 4th-axis unit installed in 2021, and a DN Solutions’ GT 3100L box guideway lathe delivered in 2023.
Commenting on the relationship, Jane Sommerville, Bowers & Jones’ Managing Director, says: “We have built strong relationships with Mills CNC, and the breadth of the machine tool ranges they supply combined with the company’s first-class after-sales service and support means that Mills is invariably our first port of call.”
Under new ownership since 2020, Bowers & Jones is committed to continuous improvement. It regularly monitors and benchmarks the performance of its manufacturing operations to identify and address current and future production inefficiencies and bottlenecks. The rollout of the company’s improvement programme, initiated four years ago when the change of ownership occurred, has been instrumental in streamlining and strengthening its in-house machining capacity and capabilities to deliver sustainable growth.
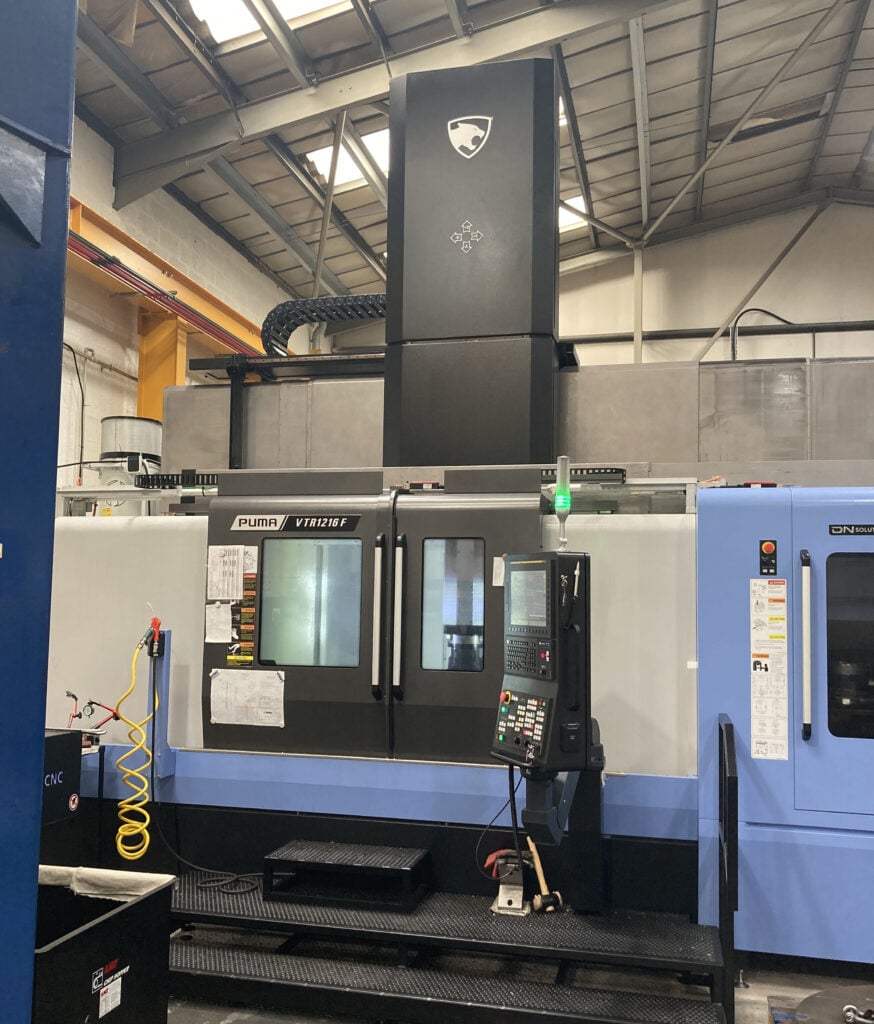
Bowers & Jones supplies its roll tooling and equipment to steel and copper mills in the UK and worldwide. The company has recently made inroads into the US steel market. Through direct sales approaches aided by a third-party agent, it is expanding its presence in North America. Indeed, the company’s new VTR 1216F investment was primarily made to meet the needs of a new US customer whose rail ‘I’ beam sections, medium bar sections and angled bar sections are used extensively in the US rail and construction sectors.
Jane Sommerville continues: “We needed a new large-capacity vertical lathe to machine large-diameter straightening rings for the customer. We won the business in Autumn 2023 and ordered the new VTR 1216F from Mills last October, expecting the machine to be delivered and installed in Spring 2024—just a few weeks before production of the rings was due to start.”
However, in early 2024, the safety and security of transporting freight through the Suez Canal were unexpectedly delayed due to geopolitical issues. “We had to revert to Plan B quickly”, remembers Jane Sommerville. “The customer’s deadlines didn’t slip, so we had to use our existing machines to manufacture the first batch of rings – basically ‘holding the fort’ until the VTR 1216F eventually arrived.”
The machine was delivered in early May 2024. To save time and minimise further disruption, it was delivered directly to Bowers & Jones’ facility from Felixstowe. Mills CNC performed its PDI, machine build, and installation on-site. Operator training followed soon after the machine was commissioned, and the VTR 1216F was cutting metal at the beginning of June.
Commenting on the machine, Jane adds: “We had been looking at investing in a vertical turning lathe for some time – partly to take pressure off an older, large-capacity Berry & Binns horizontal lathe that we had acquired some years earlier, and partly to help spearhead new business growth in the US market. We approached Mills and two other suppliers to discuss our requirements and, looking at the proposed investment package as a whole, decided to place the order with Mills.”
The FANUC controlled 50” chuck VTR 1216F machine boasts a maximum turning diameter of 1.6m and a maximum turning height of 950mm. It is equipped with a powerful 45kW 400rpm high-torque spindle, a servo-driven 12 tool ATC and an innovative quad tool holder with fast indexing that enables the use of four tools directly via the ram. The VTR 1216F delivers impressive processing speeds, improved machining flexibility, high accuracies and repeatability.
Like all roll tool types, straightening rings are performance-critical components used in metal forming processes to enable the steel to pass through one or more pairs of rolls located on stands to reduce the material’s thickness, making it uniform and consistent. Where required, straightening rings give the ‘rolled’ material additional mechanical and application-specific properties needed for the ultimate end-user.
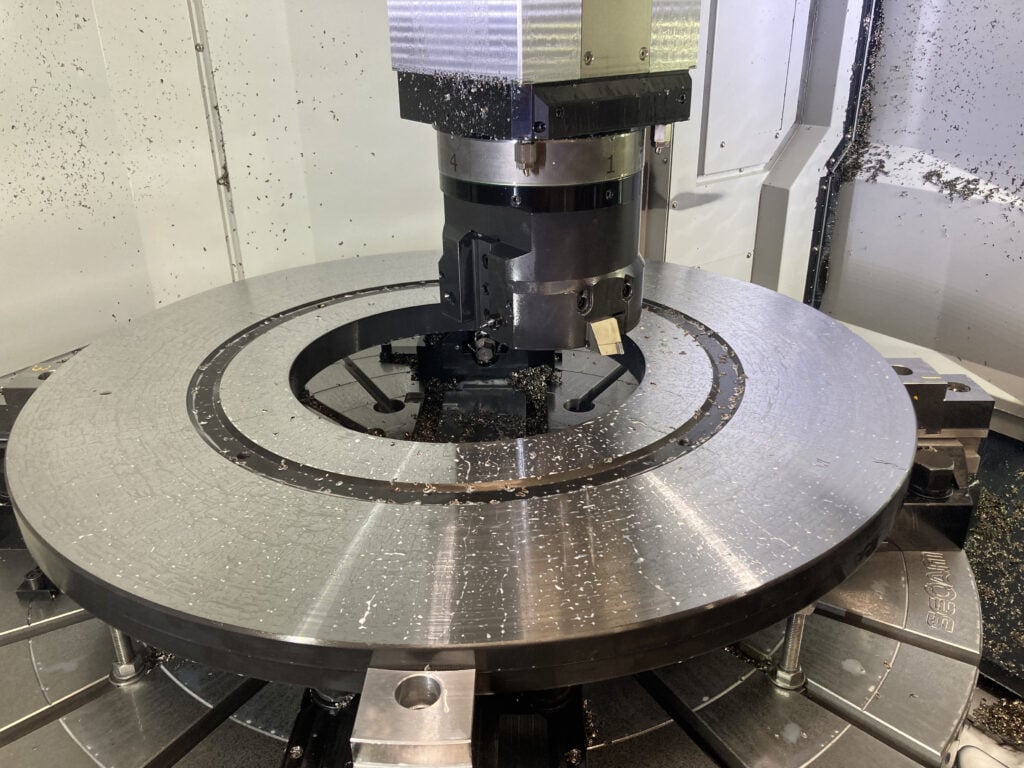
The rings process the material into bar stock, rails and structural steel beams, angle and channel stock. These are used across many industries and sectors, such as construction, rail, energy, oil and gas and automotive. The harsh and demanding environments subject rolls to high wear, thermal stress and mechanical fatigue. Consequently, they need to be monitored regularly to maintain their dimensional and profile quality and consistency, with a need for replacements over time. The straightening rings machined on the VTR 1216F are made from D2, an alloy tool steel that is difficult to machine. They are machined from solid round bars in relatively small batches, with part cycle times being long and turning operations performed at low speeds.
Roughing operations were undertaken on the company’s Berry & Binns lathe before the rings were sent for heat treatment. When the rings return, they are finish machined on the VTR 1216F to tight geometrical and dimensional tolerances with super-fine surface finishes. The heat treatment process gives the D2 rings their compressive strength, high wear resistance, toughness, and shock resistance properties—all crucially important for delivering high performance and long life in a demanding steel mill environment.
Established in 1954, the company’s knowledge of metal-forming processes is second to none. The bottom line is that Bowers & Jones’ roll tooling solutions last longer and perform better than those of its competitors. Explains Jane Sommerville: “Our high-quality designed and machined rolls may cost a little more, but they are an investment and help customers save time and money by reducing re-profiling and replacement costs, limiting potential downtime and ensuring that customers’ mills keep rolling.”
Bowers & Jones’ current five-year plan is ending, and the new five-year plan will be rolled out imminently. The company plans to upgrade its machine shop and further capitalise on new business opportunities in the US. The imminent change of administration in the United States, with its ‘Make America Great Again’ mantra, may well see the US steel market become stronger and more buoyant.
Subscribe to the MTDCNC Newsletter
Subscribe to our Newsletter today!
Stay up to date with the latest industry news and events.
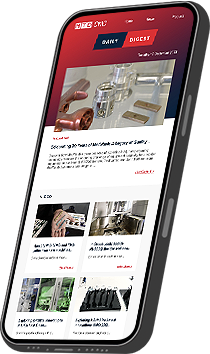