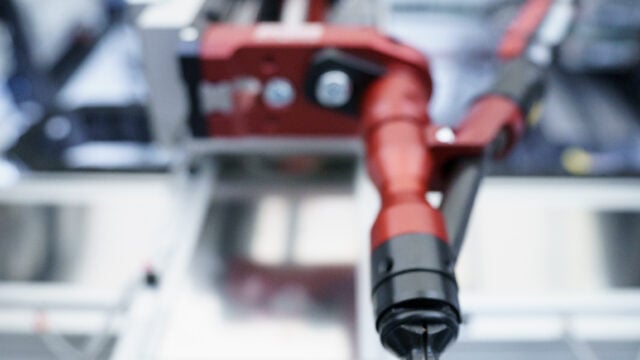
How Collaboration, Automation and Innovation Drive Growth for MTBs
Overcoming Challenges for Machine Tool Builders (MTBs) These are challenging times for machine tool builders (MTBs)…
Overcoming Challenges for Machine Tool Builders (MTBs)
These are challenging times for machine tool builders (MTBs) and their manufacturing customers. The relentless pressure to meet quality, cost and delivery demands are compounded by severe labour shortages and an urgent drive for sustainability. At the same time, companies need to harness factory data more effectively to unlock deeper insights and optimise production. With such daunting challenges at play, providing integrated solutions has never been more crucial.
Whether delivering a single machine or an entire assembly line, MTBs must incorporate an expanding array of technologies. Each build might require a collaborative robot (cobot) or similar light automation solution, tightening tools, visual inspection cameras, screw-feeding systems, electrical testing equipment, data analytics and more. Imagine shopping for every item on your grocery list from a different store. That’s the daily reality MTBs face through having to source equipment from separate suppliers. They are left juggling the complexities of programming disparate systems that lack commonality, while having to contact numerous suppliers for support. This fragmented approach leads to frustrating time losses, stifling flexibility and speed at a time when agility is paramount.
“MTBs frequently find themselves hindered by the variability of multi-supplier setups, resulting in unnecessary production delays and insufficient time to fully explore solutions or understand their true potential,” explains Alexander Hale, Product Manager for Desoutter UK&I. “It’s time to change strategy and adopt a holistic approach for equipment integration and collaboration.”
Historically known for their fastening tools, Desoutter offers a rapidly growing range of solutions encompassing assembly, automation, data analytics, process control, worker guidance, smart tooling, visual guidance and system integration – all underpinned by deep expertise.
By providing both off-the-shelf and customised solutions, Desoutter simplifies supplier selection and interaction for MTBs. Able to provide and support a wide array of systems and solutions across an entire production line, Desoutter gives MTBs the tools to do what they do best. “We’re focusing more than ever on comprehensive line solutions, not just station-based systems,” Alexander explains. “While we’ve always provided both, modern production environments require end-to-end solutions that can handle the full scope of manufacturing, including the wealth of resultant data. This shift enables us to support MTBs in building lines that are more flexible, efficient and adaptable to their customers’ evolving needs.”
This expanded focus, combined with a reputation for knowledge-led, consultative services, has deepened the relationship between Desoutter and MTBs, with companies now engaging them at a more strategic level. “Being involved from the outset allows us to understand the project goals, pinpoint bottlenecks and recommend the right solution(s) as early as possible to future-proof decisions,” says Alexander. “Our aim is to empower MTBs to focus on what they do best, while we manage the complexities of integration.”
With such a compelling proposition, it’s no surprise that MTBs are eager to leverage Desoutter’s expertise. For example, ALPHR Technology formed a strategic partnership with Desoutter to further its mission of delivering advanced automation and end-of-line testing solutions to industries including automotive, medical, aerospace and electronics. ALPHR’s partnership with Desoutter is built on a shared commitment to innovation, efficiency and sustainability, says Alexander. “Integrating Desoutter’s fastening solutions, backed by our global services capabilities, ensures higher operational efficiency, reduced downtime, and improved product quality across ALPHR’s manufacturing operation – in turn, helping its customers stay competitive in fast-evolving markets.”
Many products an MTB might choose to integrate into a project will generate and store valuable data. However, these technologies often function in siloes, leaving companies struggling with disconnected systems. While systems may ‘talk’ just enough to keep production moving, the vast potential of this data remains untapped – a huge missed opportunity to drive greater efficiency and insight.
If an MTB wants to look at historical production data, such as which camera captured how a particular product was assembled or which station completed electrical testing, they face a labyrinth of disconnected information. This lack of integration makes it hard to trace the production history of a single part or identify process improvements without heavy manual effort. “When a new production line is implemented, that’s often the last time it’s evaluated in-depth. We have all this data but little thought is given to how it could be used beyond basic operation or troubleshooting specific issues,” says Alexander.
While Desoutter continually explores how to make its own technology more interoperable, it is also working to help create a connected customer ecosystem that integrates all relevant equipment on a line. “With our connected ecosystem, production data isn’t hidden in silos. Instead, it’s gathered, made accessible and analysed for actionable insights, allowing MTBs to continually enhance line efficiency and output,” Alexander adds.
Desoutter’s powerful software solutions take this even further, incorporating insights gained from decades of integration experience. Demeter automates the collection, processing and analysis of production data to improve cycle time, make continuous process improvements and understand production trends to improve long-term efficiency. Pivotware is an advanced process control and worker guidance system that helps companies shift from assumptions to data-driven decisions. The system provides transparent processes and a reliable information source, with assembly errors immediately detected and remedied thanks to real-time feedback. “These systems maximise the value of our tools while bridging the gaps between different supplier’s equipment,” Alexander says. “We recognise that MTB’s expertise lies in manufacturing, not in data analytics. Our key is to take data that MTBs already generate and present it in a way that naturally drives improvements.”
Leaner supply chains, increased automation and ever-rising expectations for quality and speed mean that MTBs must be agile and efficient. Desoutter’s unique combination of connected assets, process control, data-driven solutions and system integration equips MTBs with the tools and guidance they need to deliver high-performance machines without the headache of fragmented sourcing.
“Times have changed. Manufacturing has changed. Desoutter has evolved, and now MTBs must adapt to remain competitive,” Alexander concludes. “With a partner that understands both the complexity of production and the power of integration, MTBs can meet today’s demands head-on. We’re here to make sure they – and their customers – are positioned for growth.”
Book a demo with us to see if we can:
Contact us here – https://www.desouttertools.com/en-gb/contact-us
Stay up to date with the latest industry news and events.
Be first to see all the updates from MTDCNC
Our newsletters frequency varies dependant on content
All the latest deals from the industry feature on our newsletters