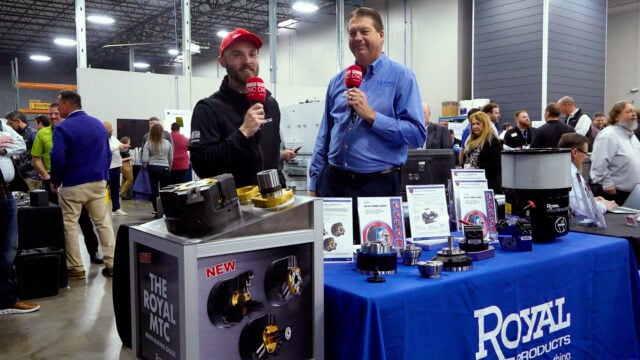
Partners like this keep the industry moving forward!
Royal Products are known for their workholding – and now we know about their incredible partnerships…
US-based Air Turbine Technology Inc. has introduced its latest innovation, the Air Turbine Spindles 601 Series, a high-speed spindle designed to significantly boost productivity, reduce costs, and provide consistent performance in today’s competitive manufacturing environment.
The new 601 Series Spindle combines high-speed cutting performance, energy efficiency, and ease of use, making it a valuable addition to any modern machine shop. Offering speeds from 40,000 to 90,000 revolutions per minute (rev/min), the 601 Series is ideal for industries requiring precision and speed, particularly in micro-machining applications. This innovative spindle is built to optimize tool performance and extend tool life, ultimately leading to significant cost savings.
At the heart of the 601 Series Spindle is Air Turbine Technology’s patented Governor technology. This breakthrough system ensures that the spindle maintains constant high-speed performance, adjusting the airflow on demand to keep the spindle operating at peak performance during the cutting process. With the ability to generate up to 0.2hp (0.15kW) of power, the 601 Series delivers ample power for micro tools, while the company’s range includes spindles capable of up to 1.4hp (1kW) for larger applications.
Unlike traditional CNC spindles, which can slow down and underperform during demanding tasks, the 601 Series maintains high-speed cutting capabilities, significantly reducing cycle times by up to six to 10 times compared to standard spindles operating at 6,000 to 20,000 rev/min. This ensures more efficient production and optimal surface quality while minimizing the risk of tool breakage.
The direct-drive design of the 601 Series Spindle ensures it operates without generating heat, which preserves accuracy during extended use. With just two moving parts, the spindle is remarkably low-maintenance, eliminating the need for regular servicing and minimizing downtime. The spindle’s ability to function at high speeds without thermal growth ensures precise and reliable operation, with a consistent 2µm accuracy.
Installation is quick and easy, with minimal downtime required to retrofit any CNC machine to a high-speed system. Connecting to a 90psi (6.2 bar) air supply is all that’s needed to convert standard CNC machinery into a high-speed powerhouse. The spindle can be installed via fully automated loading or manual connection, offering flexibility for different production setups.
The 601 Series also enhances versatility with a 50mm extended barrel, which allows access to tight workpiece areas, including pockets, angles, and hard-to-reach spaces. This feature makes the spindle ideal for machines with limited Z-axis travel and those utilizing 360-degree five-axis programming. Additionally, the spindle eliminates the need for long cutting tool stick-out, which can lead to vibration, tool breakage, and poor surface quality, ensuring smooth and efficient operation.
By streamlining production and eliminating the need for secondary operations, the 601 Series spindle optimizes tool performance and extends tool life. No lubrication is required, ensuring cleaner, contamination-free parts, which is particularly beneficial for industries such as medical and food manufacturing.
The 601 Series Spindle is available with popular taper options, including HSK-A63, CAT40, BT40, BT30, DIN30, DIN40, and 20mm JS straight shank, allowing it to be used with virtually any spindle system. This makes the 601 Series highly adaptable and a great choice for a variety of machining operations.
For more information on the Air Turbine Spindles 601 Series or to inquire about how it can improve your machining process, please contact Air Turbine Technology Inc. today.
Stay up to date with the latest industry news and events.
Be first to see all the updates from MTDCNC
Our newsletters frequency varies dependant on content
All the latest deals from the industry feature on our newsletters