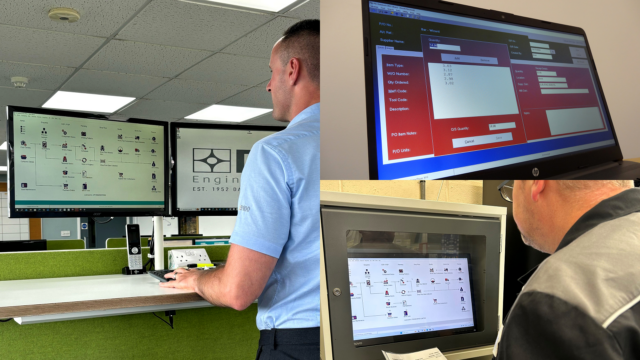
Streamline quoting and your machine shop.
In the latest PSL Datatrack newsletter; PSL Datatrack, a flexible and modular production control system for…
PSL Datatrack, a renowned provider of production control software for subcontract precision engineers, has unveiled a series of new off-the-shelf Status Boards, providing users with an immediate solution to enhance their production visibility and drive profitability.
Status Boards have been a popular feature of PSL Datatrack’s modular system for many years, trusted by manufacturers to deliver clear visual instructions to all departments on any aspect of production. Traditionally, these boards have been tailored to meet the specific needs of each customer, ensuring that they see only what is most relevant to their business.
The new release, however, introduces a simpler entry point: four ready-to-use boards that offer instant access to crucial production metrics, ideal for smaller businesses or those who may not yet have clearly defined requirements, but know they need a clearer overview of their daily activities.
Each of the new Status Boards provides valuable insight into different areas of production control, designed to tackle three prevalent pain points among subcontractors. These are a constant lack of time, management of sales and maintenance of a steady cash flow.
The first board focuses on live works orders, giving office teams a clear, real-time overview of the customer order book. This display enables staff to monitor customer and internal stock replenishment orders at-a-glance and ultimately saves time while reducing communication bottlenecks.
With this board in place, key decision makers can stay up-to date on order statuses, easily identify any order that requires attention and respond promptly to customer enquiries with accurate information. This transparency strengthens client relationships through improved response times and service reliability which, in turn, contributes to loyalty and long-term profitability.
The next board, focused on outstanding material stock purchase orders, is an essential tool for purchasers requiring real-time visibility into material supply for ongoing production. By displaying all outstanding material stock orders on one board, users can easily monitor what materials are on order, identify any items with potential delays and thus ensure that material arrives in time to meet manufacturing demands.
With instant access to purchasing information, staff can proactively manage supplier relationships, quickly address potential stock shortfalls and coordinate with production teams to minimise disruption. This level of oversight helps avoid costly downtime due to missing materials and keeps production schedules on track, resulting in greater efficiency and lasting profitability.
The third of the new boards offers invaluable insight for team members managing customer orders and inventory by highlighting components that have been allocated to specific works orders, but remain undelivered to the customer.
This visibility is especially important from an invoicing perspective, as an invoice cannot be generated until a delivery note has been created and processed for the customer. By monitoring these undelivered components, however, users can proactively manage shipments and therefore reduce invoicing delays, helping to streamline cash flow and boost profits.
The final board is the Work To List, a critical display for shop floor staff that provides a clear, organised view of what they should currently be working on and which job is next. Utilising data from the powerful Sequential Scheduler module, this board provides a structured roadmap, allowing employees to focus on the most urgent tasks and ensuring that resources are directed where they are needed most.
This immediate visibility empowers individuals to efficiently plan and manage their daily workflow, reducing the time spent determining what they should be doing and enhancing productivity. By ensuring that high-priority jobs are handled promptly, this board supports long-standing client satisfaction and helps the business maintain a strong reputation for reliability. Increased profitability is the ultimate result, thanks to minimised idle time and the reduced risk of missed deadlines.
As well as the clear immediate benefits of running the new Status Boards, each also offers significant flexibility for future customisation. Customers can opt to refine or expand them with custom metrics, colour-coding adjustments and/or new layouts when the time is right.
According to Geoff Gartland, Managing Director of PSL Datatrack, the new boards address a common need among precision engineers for clear, concise information without an initial commitment to customisation.
“Our goal with these new boards is to give businesses a straightforward starting point. We understand that some organisations want live production data, but may not yet know precisely which metrics are most valuable to them,” Geoff explains. “With these off-the-shelf boards, users can see real-time production information immediately, assess their needs and then consider further customisation when and if their requirements evolve.”
The release of the new Status Boards therefore stands as a testament to PSL Datatrack’s ongoing mission to support subcontract precision engineers in achieving efficient, data-driven production control in an increasingly digital industry.
As Geoff concludes: “Visibility and accessibility of data are critical for our user base. With these new Status Boards, we’re making it easier than ever for businesses to start leveraging real-time data for better operational control and, therefore, greater profitability.”
For more information, visit www.psldatatrack.com or contact PSL Datatrack, Lily Hill House, Lily Hill Road, Bracknell, Berkshire, RG12 2SJ, Tel: +44 (0) 1344 827312, Email: sales@psldatatrack.com
Stay up to date with the latest industry news and events.
Be first to see all the updates from MTDCNC
Our newsletters frequency varies dependant on content
All the latest deals from the industry feature on our newsletters