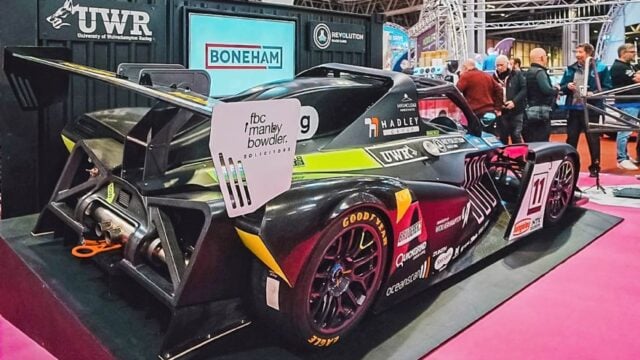
NCMT Continues Sponsorship of University of Wolverhampton Racing for 2025 Season, Supporting Innovation in Motorsport and Engineering
NCMT, a leading machine tool supplier, has reaffirmed its commitment to fostering talent and innovation in…
A new, 5-axis version of the existing Makino Slim3n vertical-spindle machining centre (VMC) was showcased at the last EMO machine tool exhibition in Milan (4th – 9th October 2021). Its focus is on high-volume production of complex parts and the machine is available with an optional automatic twin pallet changer (APC). Availability of the Japanese-built machine in the UK and Ireland is through sole agent NCMT www.ncmt.co.uk
The production centre is FEA-optimised with a fixed, 600 x 400 mm table to maximise the working envelope (500 x 400 x 500 mm) and provide structural rigidity for heavy payloads. Combined maximum weight of the component and fixture is 400 kg. High productivity is ensured by up to 20 m/min cutting feed rate in all orthogonal axes and 50 m/min rapids.
The tall machining area makes the VMC not only compact but also the only machine in its class able to accommodate vertically-oriented fixtures. A short spindle overhang increases the structure’s overall torsional stiffness and reduces vibration to enhance cutting performance.
The Makino HSK-A50 spindle, having constant pre-load, multi-plane balancing and reduced thermal growth, is designed for rigidity and high speed running. Two specifications offer 16,000 rpm /15 kW / 36 Nm as standard or optionally 8,000 rpm / 18 kW / 80 Nm to cater for a wide range of machining applications. The standard 26-pocket magazine of the automatic tool changer with integral door delivers smooth, fast indexing to support high productivity.
In the 5-axis version, the Slim3n VMC gains a 2-axis CNC rotary table and trunnion arrangement, with a Fanuc Series 0i-MF control providing complex machining possibilities by interpolating up to four CNC axes simultaneously. A 4-axis machine version, with twin drive to the trunnion but without a rotary table, may be specified for machining heavier components or taking deep roughing cuts.
The coolant system has also been configured for the production environment, with nozzle and flush coolant as standard and a through-spindle coolant option. A chip conveyor can be integrated at the rear of the machine if the volumes of swarf generated are large.
In the APC version of the machine, pallet size is 550 x 380 mm and indexing time is around 4 to 5 seconds, depending on payload. Numerous other automation options and turnkey configurations are offered.
Be first to see all the updates from MTDCNC
Our newsletters frequency varies dependant on content
All the latest deals from the industry feature on our newsletters