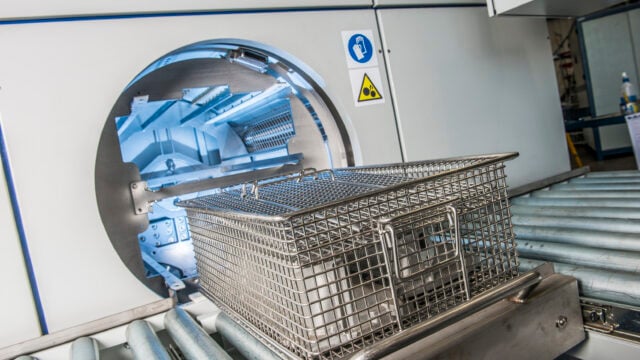
30th Anniversary for MecWash Systems!
MecWash Systems, a pioneer in industrial parts washing technology, is celebrating its 30th anniversary. This marks…
MecWash Systems, a pioneer in industrial parts washing technology, is celebrating its 30th anniversary. This marks an exceptional journey of innovation, customer focus and commitment to excellence. During this period the company has established itself as a global leader in providing bespoke aqueous parts washing solutions to meet the most stringent demands of manufacturers.
Working alongside some of the most prominent names in manufacturing such as Rolls-Royce, Brompton Bicycle, BAE, Eaton, JCB, Husco, Renishaw and Jaguar Land Rover; MecWash has developed component cleaning systems for the most complex applications. The UK based manufacturer has built unique insight and expertise for solving cleaning challenges across a spectrum of industries, including aerospace, automotive, fluid power, defence and medical.
Early MecWash
MecWash originated as a spin off from an impregnation business and was started by Paul and Steven Young, in 1993. Originally based in Gloucester, the business moved to Tewkesbury in 1998 and then relocated to the other side of the M5 junction in 2005 to its current facility.
John Pattison acquired the business and became managing director in 2008 and has overseen the growth and the progress of the technology since then. John said: “I am delighted to be part of the MecWash story, and I am excited to see the opportunities for MecWash to develop over the coming years. There have been challenging periods of economic uncertainty during my tenure here, but MecWash is stronger than ever.
“We think that 30 years is a sign of maturity and it is remarkable to see what MecWash has achieved. Our bespoke parts washing systems are now used by the world’s leading manufacturers. We are confident of building on our success over the decades to come.”
The company’s unwavering commitment to sustainability is evident in its focus on aqueous systems, designing and manufacturing durable machines with minimal environmental impact. MecWash machines are built to withstand the rigors of demanding industrial environments, ensuring years of reliable performance.
MecWash Evolution
Aqueous washing has progressed enormously during MecWash’s lifespan. Thirty years ago, solvent systems were ubiquitous in industry and many engineers were very wary of aqueous cleaning. This has changed substantially with many major manufacturers solely relying on aqueous cleaning and solvents being avoided wherever possible due to environmental and H & S concerns and the regulatory burden.
This evolution was partly driven by environmental regulations such as the 1999 EU Solvent Emissions Directive, that came into full force in 2007, causing a surge in demand for aqueous washers. It was also aided by the substantial improvements in aqueous washing chemistry and technology. MecWash has played a key role in the development of the UK aqueous washing industry. The company has consistently pushed the boundaries, developing the most sophisticated precision parts washing machines.
The first machine produced by MecWash was the MPS. The Mini, Midi and Maxi systems (small medium and large sizes) followed shortly after. These machines offered spray and flood washing, plus rinsing and hot air drying. The Midi evolved to include ultrasonic washing and vacuum drying and became the cornerstone of MecWash’s range. There are hundreds of Midis in use today throughout the UK and other engineering nations. With this system, MecWash’s reputation for solving the most difficult washing challenges was established.
In 2006, the Solo was first produced as a cost effective spray only interstage washer, before the mid-market general purpose Duo system was added in 2007. Throughout MecWash’s life a variety of special purpose system have also been developed, eg a turbine blade washer, a pipe washer, a strip metal washer and various large and complex one-off systems.
In recent years the Mini, Midi, and Maxi have been modernised to the MWX300, MWX400 and MWX600. These machines incorporate greater functionality, easier maintenance and the latest connectivity, for “talking” to customer systems or for cloud connections.
Embracing Technology
John Pattison commented: “MecWash machines have developed considerably over the last three decades. Today, the design, the build and the maintenance of the systems are very sophisticated, just like the components they are designed for. We understand the manufacturer’s process end-to-end and the different applications that require cleaning.
“System integration is part of the MecWash story. It is vital that each system in the range integrates seamlessly with other handling and ancillary equipment. Each MecWash installation is tailored to meet precise requirements of the customer.”
In addition to process and machine building skills, the team possess an unparalleled understanding of cleaning chemistry. MecWash has invested in its own laboratory at its headquarters in Tewkesbury. The site is purpose built to design, develop and formulate chemicals for common and bespoke component cleaning applications.
John continued: “Our expertise in wash chemistry is based on years of experience tailoring chemicals for the most testing wash challenges for individual customers, as well as manufacturing our own range of general wash chemicals and inhibitors,” said John.
“It is this fully rounded knowledge of all aspects of cleaning that enhances the analysis and insight our team provides, which gives MecWash the edge. Customers contact the MecWash team to find a solution to their most difficult cleaning issues, components with complex geometries, challenging substrates or tenacious contaminants,” said John.
The future for MecWash
Paul Jarrett, sales manager, said: “Since the beginning, MecWash has grown into a global force with customers and distributors in many countries including Europe, India, China and the United States. Working with manufacturers from across the world has given invaluable experience to our team and MecWash has earned a reputation for reliability and performance, and we continue to build on that.
“With our traditional applications from across manufacturing being supplemented by new industries, for example automotive electrification, there will always be new challenges for us to solve and that excites the team.
“At MecWash, we understand that a manufacturing process is only as strong as its weakest link, so we are making sure that MecWash cleaning technology embraces and supports the progress of intelligent manufacturing, continuing to provide enhanced efficiency, reliability, integration and quality for the manufacturer,” explains Paul.
-ENDS-
Accompanying photo caption:
Press enquiries: David Masson, Pepperneck, 01684 362952
General enquiries: John Pattison, MecWash, 01684 271600
Editors’ notes
Established in 1993, MecWash Systems Ltd specialises in the design and manufacture of a complete range of aqueous parts cleaning and degreasing systems for metal and plastic engineering components. Its capabilities include laboratory analysis of complex component cleaning issues and specifying or developing specialist detergents, plus the ability to design special processes and parts washers for particularly difficult cleaning challenges.
World class parts washing technology
MecWash parts washers are used in the Aerospace, Automotive, Defence, General Engineering and Medical industries. It specialises in achieving high cleanliness standards for components with intricate geometries, difficult substrates or tenacious contaminants. Its parts washers support the full range of engineering processes, including machined castings, forgings, turned parts, pressings, extrusions and mouldings.
Stay up to date with the latest industry news and events.
Be first to see all the updates from MTDCNC
Our newsletters frequency varies dependant on content
All the latest deals from the industry feature on our newsletters