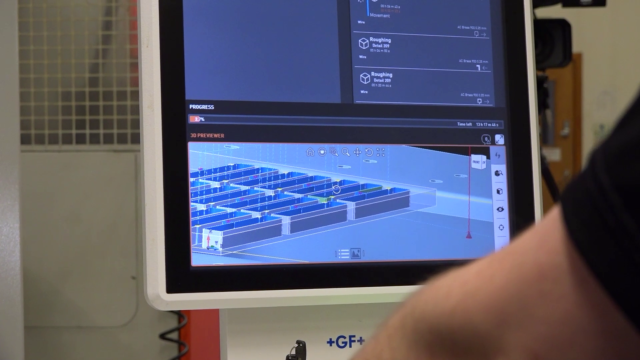
Incredible quality, speed, and productivity for Mechlam Precision with the CUT P 350 Pro from GF Machining Solutions!
After investing in the CUT P 350 Pro from GF Machining Solutions, Mechlam Precision made phenomenal…
GF Machining Solutions teams up with a cutting fluid supplier and toolmaker to create a unique machining solution.
GF Machining Solutions, Fraisa, and Blaser Swisslube have teamed up to develop the GR3 graphite machining system. Designed for wet-machining graphite operations, the system can also be used to machine other materials on the same machine…even in the same setup.
The result is an efficient process that can achieve 0.005mm tolerances while providing a healthier work environment and lower tooling costs.
Wet instead of dry? It’s a paradigm shift in mould making and for mould makers.
The entire process – from creating electrodes right through to the finished moulds – can now be performed in a single setup.
“It’s a perfect interplay between machine, metalworking fluid, filtration, and tooling,” said Martin Spencer, managing director at GF Machining Solutions (UK).
The Blasogrind GTC 7 from Blaser is the ideal coolant for this application as it absorbs the graphite dust, resulting in a much cleaner shop environment and healthier working conditions for machinists. It also reduces tool wear.
The oil film reduces the degree of contact between the graphite and the tool surface, which further increases tool life longevity.
The technology offers outstanding advantages that includes better component quality, fewer rejects, and significantly lower production costs.
Costly multi-machine operation no longer is necessary for processing various electrode materials, and the associated labour costs from setting up multiple processes, is also eliminated.
Continues Martin Spencer, “With this most recent innovation from GF Machining Solutions, we have not only solved the problem of dust build-up, but also now allow a single machine to be used for graphite, copper, and steel machining.”
All three of these materials can be machined in the same production system, without any manual intervention and with the same setup and tooling.
The system has been tested at Blaser Swisslube’s Technology Centre in Switzerland, as well as in the metal cutting laboratories of Fraisa and GF Machining Solutions. A real-world component was simulated at all three sites during testing. In addition to the various tool coatings, numerous cutting oils were compared against one another during the rough cutting and finishing operations.
The test results reveal that this system will give mould makers longer tool life, better part finishes, optimised cycle times, and substantial cost savings per machine per year.
Be first to see all the updates from MTDCNC
Our newsletters frequency varies dependant on content
All the latest deals from the industry feature on our newsletters