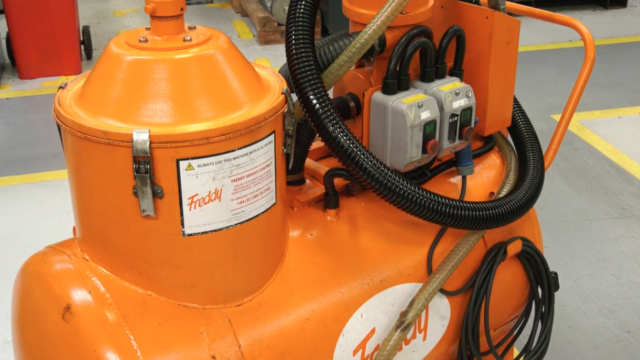
Chirton Engineering clean up with Freddy Products
In this video, MTD’s Lyndsey Vickers talks with Darren Scarr of Chirton Engineering about the benefits…
Freddy Products has now launched its latest new product line, the Freddy Coolant Health Unit (CHU). Developed in conjunction with the manufacturing team at Rolls-Royce, the new CHU is a cost-effective and remarkably efficient system for cleaning the coolant in machine tools.
The new CHU goes beyond the recycling of cutting fluid, it can also effectively clean the sump of the machine tool, removing stubborn residue and swarf to ensure all types of machine tool can be thoroughly cleaned. Unlike previous fluid extraction and recycling units, the new Freddy CHU has the ability to continuously recycle coolant at the machine, unmanned. For machine tools with relatively large coolant sumps, the CHU can recycle the coolant while the machine tool is operational, keeping spindles turning at machine shops during coolant and sump cleaning.
The ability to recycle fluid ‘at the machine’ during operation is what really sets the Pershore manufacturer apart from its competitors. This is credit to the addition of a secondary filter bag that allows the CHU to retain its consistently high coolant flow rate without ‘blinding’ or blocking-up filtration bags. This eliminates the need to extract coolant to an external IBC and then transferring the clean fluid back to the machine tool afterwards. The mobility of the new CHU is derived from its compact design, with respective length, width and height dimensions of just 1260 by 880 by 610mm. Furthermore, the 151kg (365kg when full) CHU can be easily maneuvered around the workshop on its castors, and the powerful 2kW motor runs off a single phase 110v power supply. This combination provides the ultimate flexibility for use in any machine shop.
The CHU significantly reduces the time to clean cutting fluid in machine tools – 100% recycling 2500 litres of coolant in less than one hour. This remarkably efficient cleaning rate allows manufacturers to clean machine tool fluid rapidly and efficiently, reducing the need for coolant changes, reducing fluid costs and disposal, also improving the environmental credentials for the end user. Hugely significant to the development of the CHU is the magnetic suction and return nozzles that can be placed in the machine tank to provide completely hands-free operation. This is complemented by a fully automated ‘fill’ and ‘empty’ function that allows the transition of fluid through the CHU and back to the machine without operator intervention.
The development of the CHU is the result of a 12-month joint project with Rolls-Royce that targeted ‘at machine’ fluid recycling. The aim was to recycle machine tool coolant to reduce waste and improve operator health and working conditions – in the most efficient way. The collaboration resulted in the integration of a second filtration unit whereby the fluid passes through a primary filter that catches large chips and swarf prior to passing through the secondary filter bag that captures small fines and oil residue.
The choice of filter bag combinations is dependant upon the application, but in many machine shops, the configuration of a 100micron bag for catching larger chips with a 25micron secondary filter bag is sufficient for most machine shops. However, grinding centres, specialist machines and particularly dirty machine tools may require different filtration options. The experts at Freddy Products can supply filtration bags from 1micron up to 1000microns filtration to suit the specific needs of the end user. Filtration bags from 100 microns upwards can be cleaned by hand to reduce the maintenance and running costs of the new CHU.
As well as having the facility to run unmanned, the Freddy Products CHU is available with a host of optional tools such as a Y-shaped outlet for connection to a standard discharge gun, extended length (800mm) discharge guns and a fishtail nozzle with additional extenders in 1m lengths. The optional additions enable manufacturers to use the CHU as a jet-wash inside the machine whilst recycling the coolant. Furthermore, the ability to extend lance lengths up to 3m allows operators to loosen and unblock stubborn stains and it provides access to difficult-to-reach areas where dirt and debris may be resting in ‘dead-zones’.
Commenting upon the development of the new CHU, Freddy Products Managing Director, Mr Simon Hanmer says: ““The big thing for us, really is the extra filtration that is credit to an additional basket that is placed at the top of the machine. This allows us to speed up the operation; and by putting two different filters in the machine, it becomes twice as effective.”
“Very early in the development stage, we knew we were getting great results with the new CHU. A CHU machine delivered to Rolls-Royce back in August 2019, saved 24,000 litres of coolant in just four weeks of running. That has been achieved by cleaning coolant and recycling it back to the machines; avoiding the financial and environmental cost of disposal. That is quite profound. In terms of financial numbers, the oil that is not being taken off-site and replaced is equating to a £9000 saving in a short period of time. What is equally important is that we can refurbish some existing Freddy vacuums to integrate this technology,” concludes Mr Hanmer.
For further details on the exciting new UK manufactured CHU machine from Freddy products, please contact Freddy on Tel: 01386 561113 or visitwww.freddy-products.co.uk for more information.
Be first to see all the updates from MTDCNC
Our newsletters frequency varies dependant on content
All the latest deals from the industry feature on our newsletters