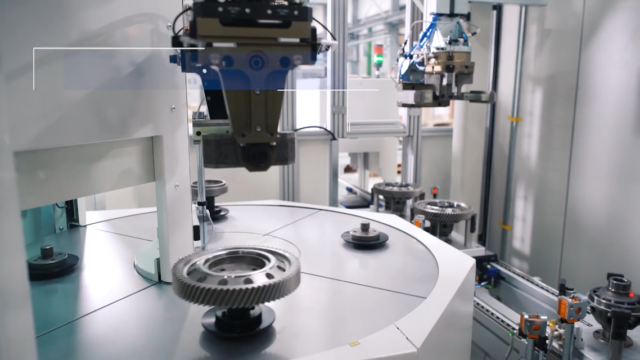
Simultaneous Cleaning & Welding in a Single Operation.
MTDCNC’s Tony Gunn finds himself with Logan Bartkovich from EMAG discussing the merits of the EMAG…
Productivity and digitization in automotive production—these are leading topics of the EMAG Group’s presence at this year’sAMB in Stuttgart.In Hall 4, Booth 4B51, the machine manufacturers will be showing, for example, their new twin-spindle pick-up turning center VL 1 TWIN. It is able to simultaneously machine two identical components. This results in an increase in unit volumes, and a decrease in unit costs. The EMAG experts will also be demonstrating how users can monitor this machine (and others) with software. An interesting new service app facilitates contact with EMAG Service in the event of technical problems or spare parts inquiries.
High-volume processes characterize transmission manufacturing: Components such as gears, cams or sleeves are produced in enormous quantities—with the (almost obvious) requirements of extreme machining precision and high cost pressure. At the AMB, EMAG will demonstrate how machine manufacturers meet these requirements with technology—the VL 1 TWIN pick-up turning center for transmission components machines parts with a diameter of up to 75 millimeters (3 inches) in diameter. EMAG is particularly focusing on running unit costs, as an employee explains in this video. For this reason, the VL 1 TWIN has two pick-up working spindles (9.9 kW / 136 Nm at 40% duty cycle) that pick up two identical workpieces from the conveyor belt, transport them into the machining area and machine them simultaneously. The crucial point is: Diameter and length (X/Z directions) of both workpieces can be readjusted independently of each other, since the headstocks can move autonomously. In addition, EMAG can link these machines with the TrackMotion automation system. The resulting multi-technology production lines produce complete cam parts, planetary or sun gears, sleeves or roller bearing rings. A detailed look at this is another focus at AMB. EMAG is exhibiting a range of machines for turning, gear cutting and grinding that can be easily linked. The synchronized interaction between the pick-up spindle and the TrackMotion automation system is crucial for the overall process. Unnecessary idle times are minimized – a feature that this film demonstrates very impressively. The individual sub-processes and the transfer of workpieces between the machine and the automation system can be observed here in detail.
Creating the Smart Factory
EMAG has made major strides in the field of digitization in recent years, as our websiteillustrates. Visitors to last year's EMO already discovered the potential of software solutions such as the “MultiMachineMonitor”, which provides production managers with a quick overview of all their machines. The “MachineStatus” program delivers key production statistics making it possible to draw conclusions about machine performance. “Both programs have been continuously developed. The focus was on customer feedback,” says Rainer Seitz, Head of Software
Development & IoT at EMAG. “That’s why we are now showing optimized versions of the program with simpler operation and a more user-friendly display at the AMB. Data from different machines can be compared in a diagram.”
Focus on Service 4.0
From the Smart Factory to Smart Service—an obvious conclusion for EMAG. The specialists at EMAG are focusing on the possibilities of using digitization to optimize service, as an employee reportsin this interview. An outstanding example of this is the EMAG ServicePlus app for smartphones and tablets. It basically works like this: In the event of a technical problem, the machine operator simply starts the app and scans a QR code on the machine. Then he contacts EMAG Service through the app, or launches a spare parts inquiry. “The EMAG engineer then knows exactly which machine is being discussed and can provide spot-on support," explains Peter Strohm, Project Manager Global Service at EMAG. “This also means that the user will always reach the appropriate contact person automatically. The entire service process becomes more streamlined and targeted.” At the ServicePlus presentation being held at the AMB EMAG Booth 4B51 in Hall 4, this and much more will be showcased. Visitors can experience the full range of the Group with its wide technology spectrum.
Pick-Up Turning Center VLC 1 TWIN
The VL 1 TWIN pick-up turning center reduces unit costs for the production of transmission components with a diameter of up to 75 millimeters (3 inches).
MultiMachineMonitor
The “MultiMachineMonitor” software provides a quick overview of all the machines in production.
Simultaneous Machining
The VL 1 TWIN has two main spindles for simultaneous machining of two identical components.
EMAG ServicePlus app
EMAG ServicePlus app: After scanning the QR code, the operator can connect with the right contact.
Be first to see all the updates from MTDCNC
Our newsletters frequency varies dependant on content
All the latest deals from the industry feature on our newsletters