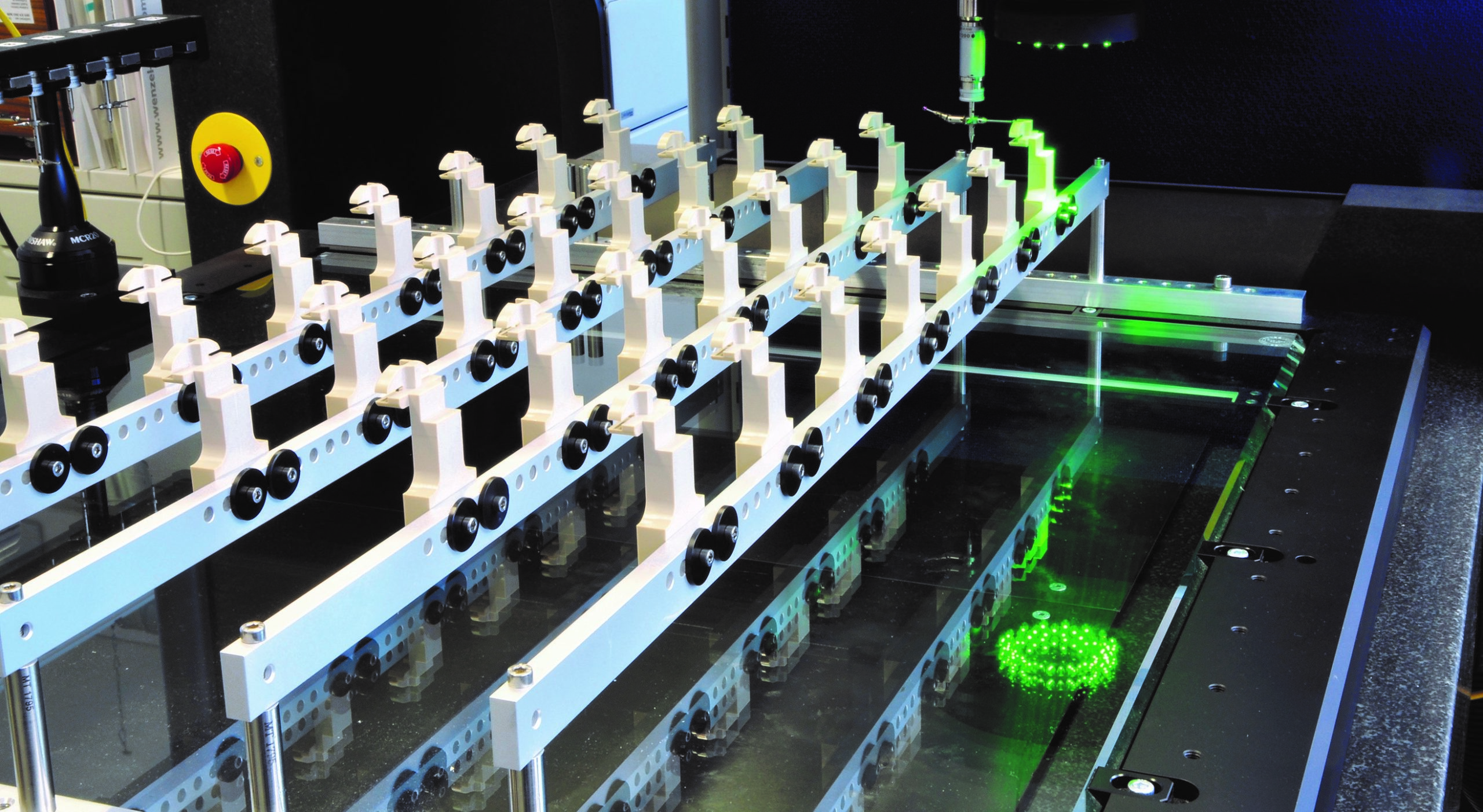
Nowhere is manufacturing’s contribution to longevity more evident than the medical industry, producing parts to prolong life. The need for precision implantation parts is reflected in the stringent requirements of the industry, including detailed traceability, compliance and 100 percent inspection to verify quality and safety. Increasingly complex elbow, knee, and hip-joint replacements are among orthopaedic implants that challenge manufacturers to remain productive while keeping quality central to workflow.
The increasing technologies to maintain a balance between efficiency and quality is proof that necessity drives innovation in medical inspection. Several complementary inspection technologies provide some level of automation, and that can be used alone or in combination to help produce challenging features — such as the smooth, shiny surfaces in implants. Multi-sensor CMMs are ideal for inspection of medical components with varied features, while specialised systems used to monitor CMMs serve the dual purposes of catching problems as they arise to support regulatory compliance.
Multiple measurement devices have traditionally been used to inspect components with a range of features, such as deep cavities, tapered holes and delicate, reflective surface finishes. However, using a handful of different inspection techniques for a single application is a disadvantage because it typically creates bottlenecks and requires regular maintenance and calibration of devices.
Programming a single CMM with two or more specialised sensors to inspect a part helps increase throughput by enabling components to be measured without repositioning, by automating sensor exchanges. As transferring parts between inspection devices and manually swapping sensors are a drain on labour, implementing multi-sensor routines saves time spent inspecting parts and eliminates some of the shop-floor travel and manual tasks linked to inspection.
Chromatic white-light, optical and tactile measurement can use a multi-sensor CMM equipped with an automated sensor exchange system. Ideal for use with delicate, reflective or deformation susceptible materials, chromatic white-light scanning sensors use focused white light to return a highly accurate measurement point. The non-contact sensors can rapidly inspect a variety of surface finishes and delicate parts. They are ideal for inspecting an artificial knee joint, for example, because while employing the right tactile probing may not damage the implant’s shiny surface, that surface will likely need to be cleaned after tactile inspection.
High-performance, non-contact optical sensors combine speed, accessibility and accuracy to capture roughly 1,000 points per second using an interferometric laser system – one of the most precise technologies for distance measurement available. Touch-trigger sensors, on the other hand, are a tried-and-true method to return a single pre-determined point of measurement. While high accuracy is a hallmark of touch-trigger measurement, this method is time-consuming and unsuitable for delicate surfaces unless the probe offers a low-force probing option.
Lights-out inspection – the backbone of Hitega’s implant quality processes
Headquartered in Germany, precision manufacturer PTF Hitega uses three Hexagon multi-sensor systems to inspect a variety of parts, including spinal implants with complex geometries. Required tolerances for the various features that include three holes into which screws are inserted during implantation, are typically within hundredths of a millimetre and are checked against a CAD model. PTF Hitega uses both optical and tactile measurement to capture features in a single clamping operation. For larger batches, the company switches to pallet measurement using two multi-sensor measuring systems to inspect products such as spinal implants made from polyetheretherketone or PEEK. Using pallets, the two systems can perform 100% lights-out inspection of 30 to 40 implants overnight.
Utilising different sensors to fit specific applications helps companies like PTF Hitega increase inspection speed. Programming two sensors for different areas of a part in the same routine speeds up the cycle if one sensor takes less time to perform inspection than the other.
The benefits of using two or more types of sensor to inspect parts for a single application vary according to factors such as part characteristics, tolerances, and material types, but specialised metrology technologies make it easier to design measurement strategies.
Given the importance of adhering to regulatory requirements for orthopaedic implant production, traceability is also a key consideration. A comprehensive history of quantifiable, traceable data is a minimum requirement that’s easier to meet with software that streamlines documentation. Traceability is optimised with CMM software that records and stores data about users who access the system, offers password protection for inspection routines and provides electronic signatures for users.
Compliance extends beyond inspection for Zimmer Biomet
Founded in 1927, Zimmer Biomet is a leading medical device manufacturer headquartered in the US. The company formerly monitored its CMMs using temperature humidity monitoring (THUM) devices and logbooks to meet quality-control demands and compliance standards set by the United States Food and Drug Administration (FDA). However, when CMM conditions exceeded the allowable range, the THUM would power down the computer that took 35 minutes to reboot.
As measurement data was lost during recovery, the company decided downtime entailed too much risk. To gain better efficiency, Biomet implemented a system that uses a network of sensors to record variations in temperature, vibration, collisions and humidity. As the parameters adhere to FDA standards, the sensors help them meet compliance. The system also offers a centralised dashboard of information.
Pleased with the results, it opted to integrate the system at multiple international locations where it co-manufactures with partners. The company integrated a cloud-based asset management system to connect machinery across production locations with a single dashboard.
Meeting stringent standards boils down to collecting and using the data throughout production. That data can also be applied using SPC to identify trends over time and determine if parts are trending toward non-tolerance. For example, for machining processes, Intelligent Machine Control (IMC) software reads data from metrology equipment and uses SPC to correct CNC controller programs directly and close the quality-control feedback loop. A range of measurement equipment, including hand-held devices, on-machine probes and stationary CMMs are compatible.
Combining technologies to build measurement systems tis easier than ever with specialised sensors that collectively measure complex parts and surfaces. Quality is non-negotiable for orthopaedic implants and employing systems capable of inspecting shiny surfaces with complex geometries is critical to efficiently achieving quality. Smart manufacturing approaches using CMM-monitoring systems and SPC software can help manufacturers remain within designated production parameters by automating aspects of production and quality assurance, while secure data acquisition and management tools ensure traceability and compliance. While each of these technologies in isolation offers benefits to quality and productivity, meeting the demands of tomorrow’s medical devices will require the flexibility and automation that only more effective use of metrology data can achieve.