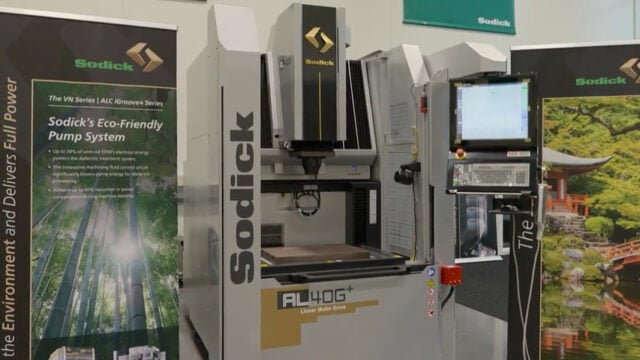
Over 33 years of world-class service and support.
It’s not just how good the product is – it’s about the service and support behind…
When global materials engineering group, Wall Colmonoy needed to modernise and upgrade its EDM machining capacity, technical capability and productivity, the multi-national manufacturer instantly turned to Sodi-Tech UK and the Sodick brand of wire EDM technology for a solution. As the industry benchmark in the manufacture of Colmonoy® surfacing and Nicrobraz® brazing products, precision castings, coatings and engineered components, Wall Colmonoy had three key areas of concern in its wire EDM department. The installation of a Sodick ALC800G Premium wire EDM machine immediately resolved them all.
As a company that manufactures components for quality critical industries such as the aerospace, automotive, oil & gas, mining and energy sectors; precision, repeatability and cut quality are a necessity for the Michigan-based company with European headquarters in Pontardawe, South Wales. It is this market position that led Wall Colmonoy to invest in the world-leading Sodick brand, a name synonymous with quality, performance and prestige that boasts an incredible reputation in all the sectors the Swansea company operates.
The challenges
With two ageing EDM machines that both had table sizes of around 300 by 400mm, any large work outside this dimensional envelope either had to be subcontracted out or turned away. Secondly, like any prestigious manufacturer, Wall Colmonoy had deadlines and capacity challenges – it needed a more productive solution that could reliably re-thread wire, run unmanned and improve cutting times. The third challenge was overcoming poor precision levels. With its existing EDM machines over 10 years old, Wall Colmonoy needed precision levels to tolerances within +/-5 microns with impeccable levels of repeatability. It was Sodick that had the answer with its ALC800G Premium wire EDM machine.
Looking at why the company invested in a Sodick ALC800G Premium wire EDM machine, Wall Colmonoy Process Engineer Kevin O’Connor recalls: “Our existing machines were ageing, and the programming side of manufacturing became very dated. We were also facing increasing maintenance costs and machine downtime.”
Supporting this opinion, Aaron Patton, EDM machinist at Wall Colmonoy says: “The programming of our EDM machines was taking too long and the cutting process was extremely time-consuming. Our management was not particularly happy about this, as they wanted parts machined faster. Another issue was capacity, we needed to put large parts on the machine, and we couldn’t do this with our existing machines. We were invited to the Sodick facility in Warwick for a day to look at available options. We were ‘wowed’ by the showroom, the hospitality and the expertise on hand to answer all of our questions. Sodick gave us all the right answers and they certainly impressed us.”
It was this visit and a longstanding relationship that were the foundation blocks to the acquisition of the new Sodick ALC800G Premium wire EDM machine. As Kevin O’Connor continues: “Sodick has had a relationship with Wall Colmonoy dating back 30 years. We went on a fact-finding tour of Sodick as well as other manufacturers to see if they could supply us with a suitable machine. As we produce our specialist alloys, we needed to know if they had a machine capable of cutting our materials. So, we took samples of our alloys to Sodick for them to prove that the machines could essentially do ‘exactly what they say on the tin’.”
Adding to this, the Business Development Manager at Sodi-Tech, Mr Tony Berry says: “I’ve had a long-standing relationship with Wall Colmonoy that probably goes back over 30 years. I received a phone call from the plant manager telling me that they were looking for a new machine. Because of our relationship, the plant manager came to me for recommendations. From there, I was invited to Wall Colmonoy to discuss options and specifications. They told us what size machine they wanted and stressed that the machine delivery date was also a critical factor. We had a machine coming into stock, so we could offer delivery in 4 to 5 weeks, which blew them away completely.”
Tony adds: “Wall Colmonoy needed a machine with a capacity large enough to accept their ever-increasing diversity of parts in both dimensions and complexity. The existing machines were too small and the Sodick ALC800G Premium wire EDM machine has a worktable of 800 by 600mm, more than double the bed size of existing machines. By purchasing the Sodick ALC800G Premium wire EDM machine, Wall Colmonoy can manage larger parts, eliminating the need to subcontract work to external sources or alternately turn work away. This will undoubtedly see the company win more business in the future.”
Another point of concern for Wall Colmonoy was productivity. As Tony continues: “The new ALC800G Premium has replaced one of the previous EDM machines and it is more productive than the two previous machines combined. This is a credit to both the productivity increase and the ability to run unmanned for extended periods overnight due to technology like the Smart Pulse electrical discharge power supply unit, Sodick’s Smart Linear technology, the fixed Jet AWT wire threading and the iGroove Plus wire rotation technology. From a programming and operational perspective, Wall Colmonoy can now process up to four different parts simultaneously in a single set-up – and even multiples of those parts. The ALC800G can accept STEP, DXF and Parasolid models files and rapidly check, convert and manufacture the programmes, saving time for the machinist, especially as this can be undertaken whilst the machine is running.”
Confirming these points, Sodi-Tech UK Technical Sales Manager, Mr Conor Plaskitt adds: “The reason Wall Colmonoy decided to invest in the Sodick ALC800G Premium supplied by Sodi-Tech is to increase the capacity of what they can cut on the machine and take on larger components. This is one of only two machines of its type in the UK and from a market perspective, it really gives Wall Colmonoy an edge over their competition with regards to the service they can offer. Couple that with the programming on the machine and the performance we can push out of it, it is a fantastic machine. We also have the technology to cut all of their exotic materials.”
Commenting upon the installation of the Sodick machine, Tony continues: “They have now had the machine for almost a year and it has performed very well. I think Wall Colmonoy are now ready to progress. As part of the free packages that we provide, we can offer advanced training that incorporates things like angle cutting, cutting compound angles, machining unusual shapes and moving on to the machining of specialist alloys, which is exactly what they do here at Wall Colmonoy.”
Looking back at the installation of the Sodick ALC800G Premium wire EDM, Aaron Patton, EDM machinist at Wall Colmonoy says: “When we took delivery of the machine there was quite a steep learning curve, but now we are running the machine confidently, the benefits are impressive. There is still an advanced course that we can undertake to further enhance our capabilities as well as maximise what we can get out of the machine.”
Concluding on the purchase, Kevin O’Connor says: “The introduction of the Sodick ALC800G Premium machine means that we can wire EDM more complex parts than we were capable of before. This will benefit our company financially as we move forward. It was undoubtedly the correct machine to purchase. Technically, it can achieve everything we need it to do. We have had excellent backup from Sodi-Tech – if we ever need anything from them, they are at the end of the phone to support us.”
Stay up to date with the latest industry news and events.
Be first to see all the updates from MTDCNC
Our newsletters frequency varies dependant on content
All the latest deals from the industry feature on our newsletters