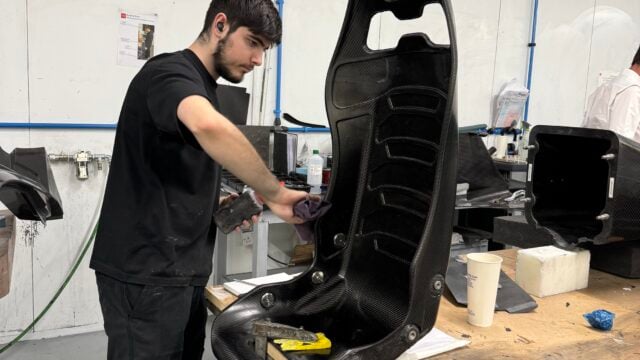
KS Composites on Fast Track with hyperMILL
Imbued in the motorsport industry since Kelvin Smith opened the doors for business in 1985, KS…
From one-off components to high-volume production, IML UK Ltd is a subcontract machining company that specialises in giving its customers exactly what they want – when they want it. With more than 25 CNC machine tools running 24/7 and 365 days a year, the Weymouth-based company has invested in the very latest 5-axis machine tools, pallet automation technology and of course, a CAD/CAM suite from OPEN MIND Technologies.
Established as a partnership that started with just two machines back in 1995, IML has invested more than £3m since 2017. Working with prestigious customers in the automotive, aerospace, medical, defence and marine sectors, the Jurassic Coast company has most recently invested in a DMG MORI Monoblock 85 with automation to service its growing customer base that demands larger components. This takes its 5-axis machine tool capacity to six machines – all with automated pallet systems.
Discussing this, IML UK Ltd Director David Zollo says: “The work on the machining side of the business is predominantly aluminium with our turning department being mainly stainless steel machining. We’ve now been doing this for 30 years, so when we began there wasn’t any CAD. We entered the market of CAD and CAM systems back in the early days and we’ve now had that CAM system for probably around 25 years. However, things have evolved and designers have changed the way they design things and jobs are getting more complicated. The parts are getting more complex and the software systems have changed too.”
“Now, we use two CAM systems. We introduced hyperMILL more recently and we are finding that hyperMILL is better on the complex parts we make – but we are now also applying it to our simple parts. For parts where there are loads of lines of code, it’s all about the re-generation. If you are designing a complex part there can be a lot of time spent re-generating the program. If you have a part that you want to design, one software package can spend a long time regenerating that program, especially if you have to make a tiny change at the end of the program – it will regenerate the program from the top all the way down. Sometimes that can be very time-consuming.”
“When you do a regeneration of a complex part that is ‘millions of lines long’, we are used to the regeneration taking forever but with hyperMILL, it will just regenerate the bit you need. This saves us a lot of time on our more complex parts. So, hyperMILL is better for programming our complex work as it is much quicker, especially when you just want to make a small change.”
Alluding to tool paths, David adds: “We just find that with CAM software cycles, the tool is always moved up and over – and back and forth with a lot of ‘thin air cutting’. It’s hard to see that ‘thin air cutting’ when you are programming, as there are so many lines of code on the screen, so it’s almost impossible to see the tool paths. When it’s on the machine, you see the machine cutting thin air when the tool is travelling up and over the part. These are the parts where you need to go back to the software and change the toolpaths.”
“When you do that and you have to regenerate the whole programme, it takes forever. If you can just regenerate that one part of the program, as you can with hyperMILL – it makes it much faster to get the part back on the machine and cutting.”
“As a company that has two software systems, we do know what we’re talking about. So, we can give an honest opinion of where we are with the two systems. With hyperMILL, the training, service and sales teams were fantastic and we found the transition from one system to another very easy. They are two completely different systems, but some similarities made the transition easier. We are now leaning more and more towards hyperMILL when it comes to our complex parts.”
“The service and applications team have been fantastic. With the evolution of things like Teams in the aftermath of Covid-19, we don’t need engineers coming to see us. We contact them and they can link into the software and see what is on our screen via Teams. This means that with just a call, we can get things sorted over the phone with OPEN MIND. Even the updates can all be done online, so it’s fantastic.”
Regarding the capabilities of hyperMILL, David says: “They do have more cycles on there, so you can now look at a part and have around 20 different cycles you can choose from and determine which one will work best for your part. OPEN MIND are launching more strategies all of the time too and this increases the number of options. Parts are forever getting more complex and you can select what you think may be the best strategy, but you then change to another strategy and save yourself an additional 10 minutes on cycle times. There is a definite advantage to having more cycles and more options available.”
Looking at the machine tools on-site, David adds: “We have 3-axis and 5-axis machines on-site as well as large and small machines – we pretty much have the full suite of technologies available to us. For this, we find hyperMILL is fantastic. Once we’ve generated a program, the posts mean that we can almost move the program from machine to machine. We can even run a job on a 5-axis and with a small change move it to a horizontal machine. A horizontal may work completely differently from a 5-axis, but once you have the tool paths in there, you can just change it around. We found that once we generate a program, we can pretty much move it to any machine. We can even take out the 5-axis stuff like certain tool paths and transfer parts to a 3-axis machine. hyperMILL gives us this flexibility”
Discussing the latest DMG MORI DMC 85 FD monoBLOCK investment that arrived in 2023, David concludes: “We have invested in this large machine as our parts are getting bigger. The larger the part and the more complex the jobs become, the more lines of code that are required. With this trend, we find that hyperMILL is the only software we will use on this machine. That is because the program files are so large and long that hyperMILL is pretty much the only system that can cope with it.”
Stay up to date with the latest industry news and events.
Be first to see all the updates from MTDCNC
Our newsletters frequency varies dependant on content
All the latest deals from the industry feature on our newsletters