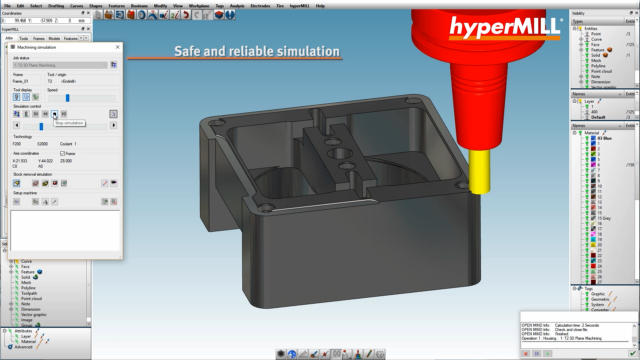
Get perfect, precise, and safe tool paths with this cool technology!
Lower machining time or better surface quality? Get the best of both with hyperMILL’s 3D machining!…
MTDCNC’s Rowan Easter-Robinson is in a discussion with Dan Johnston from KS Composites, an innovative global composite manufacturing expert that serves a variety of sectors including automotive and motorsport.
What are some of the best practices at KS Composites and how do they design and deliver some of the most challenging composite structures with a flawless finish? We’re going to walk through their new investment in hyperMILL that’s helped them cut programming time by over half. KS Composites looks at patterns of various sizes and complexities that are put into machines and then designed using 5-axis machining. They use a range of materials from epoxy tooling boards to aluminium.
Carbon component trimming allows the company to trim components and produce fixtures for various materials. This helps to create a tool path around the part without any tool marks, leading to a finished piece. With a lot of complex features, hyperMILL requires a CAM system. KS Composites aims to maintain efficiency using 5-axis contouring, which is indeed a complex tool path but has great ease of use, thus ticking off all the boxes and ensuring a high-quality product off the machine.
The company works with new starters by enrolling them into an introductory training for hyperMILL that shows them the company’s process, predefined templates, preferred tool paths and how to design and develop parts that meet the high standards set by KS Composites globally.
Be first to see all the updates from MTDCNC
Our newsletters frequency varies dependant on content
All the latest deals from the industry feature on our newsletters