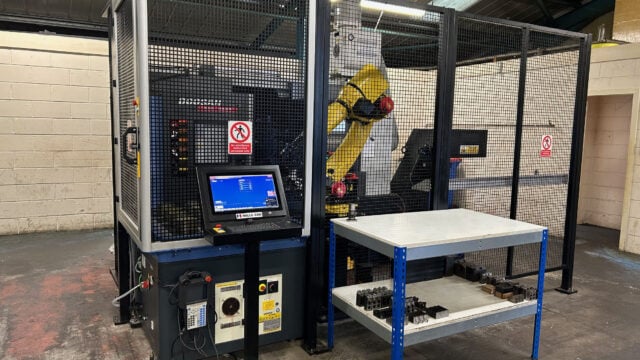
Automation investment delivers significant business benefits.
Ayrshire Precision transforms its small turned part processing operations by investing in two SYNERGi automation systems…
To meet an increase in demand for its world-class industrial engine repair and overhaul services, Aberdeen-based RWG (Repair and Overhauls), invests in two new DN Solutions’ high-performance lathes from Mills CNC to strengthen its in-house machining capacity and capabilities.
The new machine tool acquisitions, made as part of a larger capital equipment investment programme, will help the company improve its quality and process efficiencies whilst simultaneously controlling costs and reducing turnaround times.
Mills CNC, the exclusive distributor of DN Solutions’ and Zayer machine tools in the UK and Ireland, has recently supplied RWG (Repair & Overhauls) Ltd., with two new DN Solutions’ high-performance CNC machine tools.
The machines, a Puma VTR 1216M vertical turning lathe and a Puma 3100Y multi-tasking turning centre (both equipped with advanced Fanuc controls), were installed at RWG’s machine shop facility in Aberdeen in March 2024 and July 2024, respectively, and are the first DN Solutions’ machines the company has acquired in its 34-year history.
About RWG
RWG is an international, OEM-approved business that provides comprehensive repair, maintenance and overhaul services for Siemens industrial aero-derivative gas generators (used in power generation and oil and gas applications), and Rolls-Royce marine gas turbines (used in marine propulsion systems).
In short, these services, which all take place at RWG’s facilities in Aberdeen, start with the stripping down of a customer’s gas turbine or generator for cleaning and inspection purposes before the components are repaired at their Advanced Remanufacturing “Centre of Excellence” facility before being returned to the engine for reassembly.
Overhauled or repaired units are then rigorously tested before being delivered back to customers’ sites, which can be anywhere in the world.
Specific turbines repaired and overhauled by RWG include – industrial SGT-A35, SGT-A20 and SGT-A05 gas generators, and WR21 marine propulsion gas turbines.
Turbine and generator repair – RWG process
To support its repair and overhaul business, RWG has at its disposal, a well-resourced component repair facility that includes an extensive machine shop.
The in-house machine shop provides one of many integrated repair and overhaul services and processes (i.e. welding, fabrication, heat treatment, crack testing, spray coating and painting etc.), that may be required to repair a specific customer’s industrial gas turbine or generator.
During the inspection process failed and worn components are identified by RWG experts, and the decision is made as to whether they can be repaired in-house or need to be replaced completely with new parts.
If and when repair is the preferred route, the parts make their way to the machine shop for turning, milling, boring etc.
RWG’s machine shop
To meet a global increase in demand for its repair and overhaul services RWG, as part of its continuous improvement programme, constantly looks to upgrade its machine shop and the machining services it provides.
The objective throughout is to bring as many these repair services in house in order to better control quality, efficiencies, costs and lead times.
As part of its upgrade programme, the company has begun to replace older manual machines with new CNC models. (The investment in the two DN Solutions’ machines from Mills CNC is evidence of the programme in action).
Says Angus Donald, RWG’s Production Supervisor:
“We are a vertically-integrated engine repair and overhaul specialist company dedicated to helping our customers prolong the life of their gas turbines or gas generators and keep (their) life cycle costs to a minimum.
“To keep ahead of the curve and meet growing demand for our expert services we are in the process of strengthening our in-house machining capacity and capabilities to help us improve turnaround times and make us more efficient, productive and competitive.”
VTR 1216M investment
The investment in the DN Solutions’ VTR 1216M (vertical ram-type lathe), which has replaced an older, large-capacity manual borer, was made to re-machine and repair a wide spectrum of large turbine and generator parts i.e., engine casings, stator and rotor vanes, housings, shafts, seals, valves, actuators etc.
Part conditions vary from relatively new engines right through to previously re-worked and reconditioned components from older ones, and can involve the machining of parts with hard coatings as well ones with tough, welded features (i.e., Stellite) too.
Some of the parts RWG are asked to repair can be 30 – 40 years old and because there are no actual spares available from the OEM or other suppliers, the company has to use its expertise, that includes in-depth knowledge of different materials and their machinability, to deliver a solution that works.
Continues Angus Donald:
“We made the decision to replace one of our older borers with a new vertical turning lathe in 2023 and, seeing as this would be our first large CNC machine tool investment, we did our homework and approached the market to discuss our requirements with a number of machine tool suppliers.”
A visit to Mills CNC’s Campus facility in Leamington to meet up with the company’s sales and applications staff, followed by a further visit to a (Mills) customer who had previously invested in a DN Solutions’ vertical ram-type turning lathe, as well as trip to DN Solutions’ factory in South Korea, all contributed to RWG’s decision making process.
Once the exact specification and price of the machine, and the level of after-sales service and support to be provided, were agreed, RWG placed the order for the new VTR 1216M with Mills CNC.
VTR 1216M – a closer look
The VTR 1216M is a large-capacity, rigidly-designed and built (box guideway) vertical turning lathe.
The machine is equipped with a 1250mm (50”) manual 4-jaw chuck, a powerful, high-torque 45kW/400rpm/20557N-m spindle, a servo-driven 15-tool ATC and a 260mm x 260mm RAM spindle (3000rpm).
The lathe has a maximum turning diameter of 1600mm and maximum turning height of 1250mm, and a maximum table load of 8000kg.
The machine supplied to RWG also featured an auto tool setter, 70bar (high-pressure) coolant capability, a RPM60 Renishaw probe and a FilterMist extraction unit.
Says Angus Donald:
“The VTR1216M is a powerful and flexible vertical turning lathe capable of handling a range of large, heavy and awkward-shaped parts.
“Since installation, the machine has performed well and is hitting the non-negotiable, tight tied-up tolerances on the performance-critical parts we repair.
“Such has been the support and service from Mills, during and after the purchase process, that we decided to place an order with them for a new Puma 3100Y (multi-tasking) lathe.”
Puma 3100Y investment
The Puma 3100Y with its 12“chuck, 130mm Y-axis and 5000rpm driven tooling capabilities was acquired by RWG, as part of larger manufacturing repair project, to machine a series of complex, high-precision parts, in relatively small volumes, for specific engine’s combustion system.
Previously this work had been subcontracted out by RWG to a preferred supplier but, following its closure, this work has now been brought back in-house.
Rather than supplying just the machine, RWG approached Mills to design and develop a turnkey manufacturing solution to optimise the machining of three different combustion system parts that are made from C263 – a nickel-based superalloy.
The process developed by Mills was designed, developed and proved-out at the company’s Leamington Spa facility before being installed at RWG’s machine shop in July 2024.
Following the completion of an intensive training programme, conducted by Mills on-site, and covering the new machine and the newly-developed manufacturing process, everything is now in place to “hit the ground running.”
Says Angus Donald:
“We needed a smaller CNC lathe to handle these parts and required a robust and efficient machining process to maximise their production.
“Mills delivered on both counts, and we are now waiting for the green light to start production.”
Summary
Concludes Angus Donald:
“We are being approached and asked to machine and repair bigger and more complex components within ever-decreasing timescales, so it seems.
“As a consequence, we need access to high-performance machine tools that are up to job.
“The VTR1216M is proving its worth and is making us more efficient and productive. We have similarly high expectations of the new Puma 3100Y.”
Stay up to date with the latest industry news and events.
Be first to see all the updates from MTDCNC
Our newsletters frequency varies dependant on content
All the latest deals from the industry feature on our newsletters