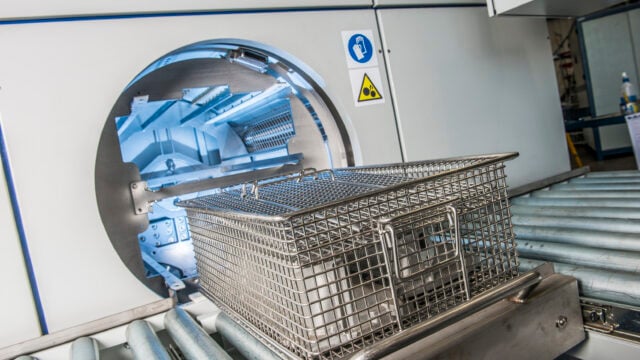
30th Anniversary for MecWash Systems!
MecWash Systems, a pioneer in industrial parts washing technology, is celebrating its 30th anniversary. This marks…
The addition of the MecWash MWX300 has made a dramatic impact at IMI Truflo Marine, increasing cleaning productivity over six times whilst vastly reducing the operational manpower required. IMI Truflo Marine noted a significant improvement in both efficiencies and the standard of cleaning which helped the business meet global demand. The historic naval valve manufacturer make flow control solutions, with over 120,000 valves in service to 24 of the world’s naval fleets.
IMI Truflo Marine contacted Paul Jarratt, sales manager at MecWash, to enquire about upgrading to a high-performance aqueous cleaning system to improve their cleaning programme.
Paul Jarratt comments: “Speaking with the team at IMI Truflo Marine, it was clear we could build a machine that would make a substantial difference to the output of the business. We discussed their current cleaning programme which consisted of two large ultrasonic dip tanks and required a sizable amount of energy and resources.
“The MWX300 was the ideal machine for application at IMI Truflo Marine. The precision cleaning and sophisticated drying processes would ensure the components are free of contaminants, preserving the critical tolerances necessary. Marine components have very tight tolerances, and even small amounts of dirt or contamination can prevent them from functioning properly,” said Paul.
MecWash works alongside companies from across manufacturing and engineering to design and build bespoke parts washing machines to streamline their cleaning regimes. The experienced team designs and builds industrial parts washers for particularly difficult cleaning challenges. Customers receive an in-house laboratory analysis of complex component cleaning issues and MecWash can specify or develop specialist cleaning chemicals when required.
IMI Truflo Marine has been a specialist in the design and manufacture of high integrity valves, actuators and pressure reducing stations for critical naval marine applications for over 60 years. In the marine industry, the process of precision cleaning is crucial for manufacturers, as high quality and adherence to regulations are essential.
Kurtis Smith, continuous improvement engineer at IMI Truflo Marine, said: “Truflo needed a machine that could provide a consistent and high-quality finish on valves in sensitive materials used in marine systems. It was important for the business that the new system could improve productivity with less manpower required in the parts washing process.
“Since the installation in 2022, the MWX300 has delivered impressive cleaning results, especially considering its size. The cleaning process has always been challenging due to the sensitivity of the parts and the mirror finish required. Previously, only three valve kits could be cleaned with a 30-minute cycle, with the MWX300, 12 kits are being cleaned within 18 mins, with a smooth and polished finish.
“The previous method was manual and required the parts to be blown dry with air guns after washing. Now, the parts are simply placed in the baskets, loaded into the MWX300 and the start button pressed. 18 minutes later, 12 kits of clean and dried parts are ready for the next operation with the minimum of manual intervention which fulfils the brief that we originally presented to MecWash,” said Kurtis.
John Pattison, managing director at MecWash, said: “The MWX300 will support the long-term durability and functionality of the components cleaned at IMI Truflo. We are exceptionally pleased to have made such an impact to their productivity with the machine speeding up the cleaning capability of IMI Truflo Marine from 6 kits an hour to over 36 kits per hour, all with the drying included.
“The reports from IMI Truflo show the immediate impact of the MWX300. These improvements highlight the results of the MecWash machines and the value that the change in precision cleaning can bring to manufacturing companies. Well-cleaned and maintained parts perform better and last longer, contributing to a more reliable operation and creating savings for the customer in the long-term,” said John.
Be first to see all the updates from MTDCNC
Our newsletters frequency varies dependant on content
All the latest deals from the industry feature on our newsletters