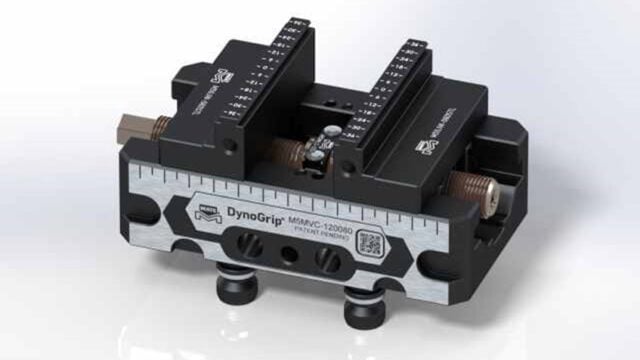
Leader extended zero-point offering with Mate Precision Technologies
Following a recent partnership agreement, the full range of Mate Precision Technologies’ high precision zero-point fixturing…
Established in Italy in the early 1960s, Tecnologie FRB designs and manufactures live centres and face drivers for turning, gear cutting, and grinding applications. The company has built an enviable global reputation in this sector, and its comprehensive product ranges are now available in the UK and Eire from workholding and ancillary manufacturing product specialist, Leader Chuck International.
Managing Director, Mark Jones, explains how FRB has built its reputation: “When Romano Franceschelli founded the company, he used his experience as a turner and exceptional engineer to initially design a live centre that would reliably address all the issues he faced as a lathe user.
“Reliability would be the best word to describe FRB. Reliability of the products, of delivery, of the services offered and the response times for any customer requirements. These are the cornerstones on which FRB has based its production. So, the reliability of a technical solution and subsequently, of a finished product, is undoubtedly linked to innovation. Innovation linked, in turn, to technological evolution within the manufacturing sector, which, in turn, drives change.”
Products started with the FRB patented 65, 80 and 85 live centre series with axial load distribution, and continuous research and development has resulted in the more recent series of 2000, 2006 for high-speed turning, and 2008 for hard turning. With high quality steel integral shafts available with or without carbide tips, interchangeable inserts and cone shaped heads means Tecnologie FRB’s live centres offer a tangible solution to manufacturing industries’ requirements. A complete range of revolving live centres is available, equipped with morse tapers in different sizes, both with standard and special features to fulfil most requirements.
The company’s constant quest for innovation has seen it excel in a wide range of mechanical processing, from conventional and CNC turning and gear cutting to the more demanding cylindrical grinding and tooth grinding applications.
Live centres for grinding are in the 92 series and include the models for pipe grinding and the dead centre series for hard metal applications. For gear cutting the 82 series live centres provide axial and radial load with roller bearings.
A comprehensive range of face drivers for turning, grinding and gear cutting applications is also offered, with FRB having developed its first model back in 1965. “The range of face drivers can fit any workpiece holder from 5 to over 300 mm diameter,” explains Mark Jones, “from the classic spring-operated system, right up to the most advanced hydraulically powered system. FRB patented balancing and holding system, which is completely mechanical and technologically state-of-the-art, always guarantees absolute reliability, constant repeatability of results and unparalleled holding capacity.”
Thanks to the introduction of face drivers, turning and grinding processes have undergone a number of innovative improvements that have resulted in shorter cycle times for many workshops. The driver acts directly on the workpiece so the cutting tool or abrasive wheel has increased access to the whole part. With none of the raw material being held in a chuck or similar device it is often possible to finish parts in one hit, minimising any potential datum errors from repositioning for second operations and so on.
At its plant in Bologna, Italy, highly qualified staff use an advanced manufacturing system to produce FRB Live Centres, from the original series right up to the latest versions for different axial loads from classic turning and gear cutting to the most demanding of external grinding and gear cutting production. FRB Face Drivers are also produced here, with products to satisfy the classic need of a spring-loaded centre to the most advanced fixed centre systems.
New state-of-the-art machine tools, such as twin-spindle lathes with three automatic tool changers and bar feed, are used for turning and milling. These can carry out multifaceted machining tasks aimed at producing complex components supported by the inhouse CAD/CAM team.
The grinding department is equipped with multi spindle machines for external and internal machining in a single setup to support production and manufacturing requirements, achieving the necessary geometrical tolerances for both form and finish.
Finally, a fully automated warehouse system ensures stock levels are matched to demand. With impressive stock levels of standard products and a flexible manufacturing process that can turnaround special bespoke parts within minimal lead times, customers can be sure that promised delivery schedules are achieved.
Mark Jones concludes: “The values instilled by its founder, Romano Franceschelli, characterise FRB to this day. The sense of family, the sharing of each challenge and a common vision based on sociability and the desire to discover innovative solutions, makes the FRB team unique and efficient. Not only their products, but also their know-how and experience regarding the optimisation of work cycles in turning and grinding will benefit customers both in the UK and Ireland.”
Be first to see all the updates from MTDCNC
Our newsletters frequency varies dependant on content
All the latest deals from the industry feature on our newsletters