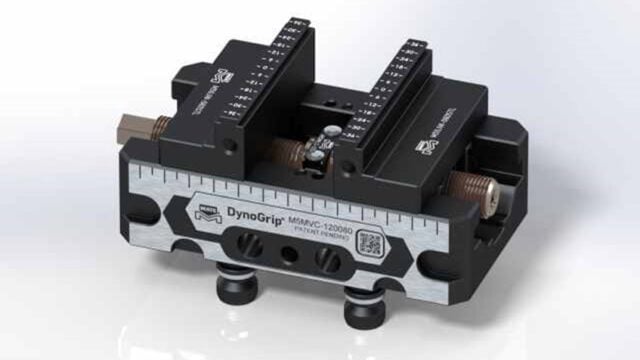
Leader extended zero-point offering with Mate Precision Technologies
Following a recent partnership agreement, the full range of Mate Precision Technologies’ high precision zero-point fixturing…
Following a recent partnership agreement, the full range of Mate Precision Technologies’ high precision zero-point fixturing is available in the UK from workholding and machining efficiency specialist, Leader Chuck International.
Being one of the latest players to enter the zero-point fixturing market, Mate Precision Technologies was all too aware of the need to bring significant advantages over the competition when it launched its next generation Dyno range.
Consisting of DynoGrip vices, DynoLock base plates and DynoMount tombstones, the ethos behind the range stems from Mate targeting manufacturing efficiencies within its own workshop. With an enviable reputation for producing high quality punch press and pressbrake tooling for manufacturers across the globe, the company employs around 300 highly skilled staff at its manufacturing facility in Minnesota, USA. So the need for machining efficiency gains comes from worldwide competition.
Extensive trials of the previous generation zero-point systems, available from established suppliers, under real life production operations highlighted a number of limitations that have been addressed by these new products from Mate.
Leader Chuck’s Managing Director, Mark Jones, explains: “With Mate’s extensive knowledge of the high quality tool steels and the fine tolerances used to produce its tools for sheet metalworking, it is only logical that the same materials and processes are used for the Dyno range of fixturing. It is why the company offers a ‘zero wear out forever’ policy across the range with a 100% unconditional customer satisfaction guarantee.”
Mate DynoGrip self-centring vices are engineered to shorten setup time and reduce process variability. Two zero-point four-stud engagement patterns are offered, 52 mm and 96 mm, that are compatible with other systems or can be mounted directly to the machine table via toe clamps or bolted through the body.
Available in 13 sizes, the vices feature quick change jaws with an innovative ‘click-lock’ system for quick setup, and a 45o angle on the top jaws to pull the workpiece down into the vice body for maximum rigidity during heavy cuts. They can also be quickly reconfigured to grip outwards with the jaws holding the internal walls of the component or billet.
Production flexibility is further supported by the vices ability to hold two parts at the same time. “With a fixed centre jaw and the quick removal of a locking pin the vice becomes dual-station. Even dissimilar sized parts can be securely held simultaneously with absolute confidence,” Mark Jones says.
With 11 size and shape variants there is a DynoLock base to suit any machining application. These quick-change workholding bases are the foundation of the workholding system and the key to superior productivity. The product mounts to the machine bed, tombstone, pyramid, or riser, and offers best-in-class accuracy and repeatability with a superior holding force. “Mate takes the term zero-point very seriously,” Mark Jones states. “DynoLock has what it takes to securely hold your vice, whether you change the same vice repeatedly or exchange it for a different one. DynoLock reduces your machine setup times and keeps your spindle cutting.”
For increased volume production applications and higher part loading density, DynoMount three- and four-sided tombstones are available for use with Mate DynoLock 52 and 96 bases. Using a chambered design for weight reduction, Mate tombstones also include a hoist ring lift connection for easy loading and unloading. Like the rest of the Dyno range, they feature Mate’s QuickSpecs 2D bar code tag for real-time access to full product specifications, CAD files and potential integration into your business systems. Direct-to-table mounting, and custom mounting bores are also available. They are also compatible with some competitor workholding bases when used with applicable bushings and hardware.
Mate’s mission is to personally respect, support and inspire metalworking professionals around the world with high-quality products and services for factory productivity. Mark Jones concludes: “In the design and build of these units Mate wanted to match or exceed the tolerance levels achieved by the leading machine tool suppliers. In short, if you are approaching or aiming for better than single digit micron tolerances and consistent repeatability of your machined components then this is the only zero-point system for your workshop.”
Be first to see all the updates from MTDCNC
Our newsletters frequency varies dependant on content
All the latest deals from the industry feature on our newsletters