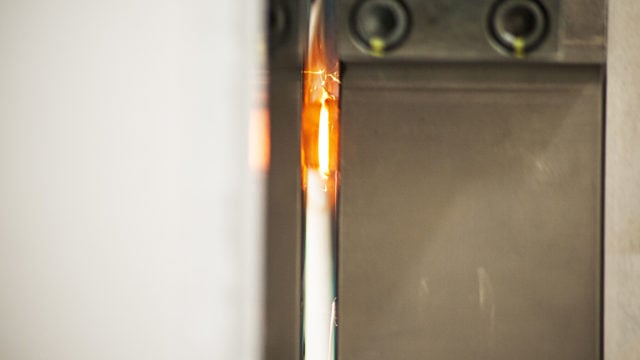
Thompson Friction Welding : Subcontract Linear Friction Welding
What is Linear Friction Welding? Linear friction welding is a solid-state joining process. The technique involves…
It is well known that automation boosts productivity but what about when robotics is added to conventional machine tools?
Our Platinum system partner CNC Robotics has recently worked on a solution that had astounding results. Through adopting automation at the end of a Mazak Integrex machine during the lockdown period one of their customers tripled production. Jason Barker, Chief Technology Officer at CNC Robotics explained “The company works nine and a half hour shifts and expects each machine to work for around eight of those hours. After adding the robot, production can be maintained for up to twenty-four hours a day and across the weekends.
A typical package from CNC Robotics includes the KUKA robot, its enclosure and a purpose-designed fixture to load and remove the parts, together with the programming and installation. The resulting increase in productivity means that the systems can repay the investment in a few months or even a few weeks.
The increased production can necessitate additional investments in swarf-handling equipment, such as a high-capacity swarf conveyor to remove all the excess material that will be produced and a swarf compactor to compress the chips down to a more manageable volume when machines are running over the weekend.
Automating machine tending allows you to keep up with demanding quality requirements on the workpieces being produced, increased productivity and the highest precision from KUKA robots mean that even the tightest of delivery times are met with ease.
In addition, industrial robots are usually easier to repurpose if they aren’t required by a machine tool any longer. CNC Robotics sets up its systems so that they can be removed from the equipment in around five minutes, either to be used on another machine or in a completely different area of automation.
Robotic systems can give companies time to train and upskill their staff in more productive ergonomic work. By removing the need to have operators constantly loading and unloading machine tools, time can be made available to increase their range of skills, for example, by teaching them to use a wider range of equipment or by allowing them to add new abilities like CADCAM programming. The extra time can also be used to put more emphasis on process control and optimisation, so allowing general efficiency to be improved, and potential problems to be anticipated and resolved more effectively.
There are so many benefits to automated machine tending, as well as all the production value you could also avoid a large cost out lay and hold on to capital within the business by using KUKA’s robot lease solution. You can save up to 60 percent by leasing a robot and other benefits include flexible lease terms and warranty for parts.
With KUKA’s robotic expertise and CNC Robotics innovation and breadth of knowledge for robotic systems provide reliable efficient solutions for automated machine tending.
Jason from CNC Robotics concludes “The experience we have gained over ten years of machining with robots gives us a unique perspective when developing systems for machine-tending,” claimed Jason. “We approach machine-tending projects with the same can-do attitude that we do our other work – we will make the system work successfully for the customer no matter what challenges we may encounter.
For more information on Machine tending Solutions please contact.
Area Sales Manager and Machine Tending Sector Manager Jonathan Pick by emailing jonathan.pick@kuka.com or by phone T: 0121 505 9970 Mobile: +44 7487 666022
Be first to see all the updates from MTDCNC
Our newsletters frequency varies dependant on content
All the latest deals from the industry feature on our newsletters