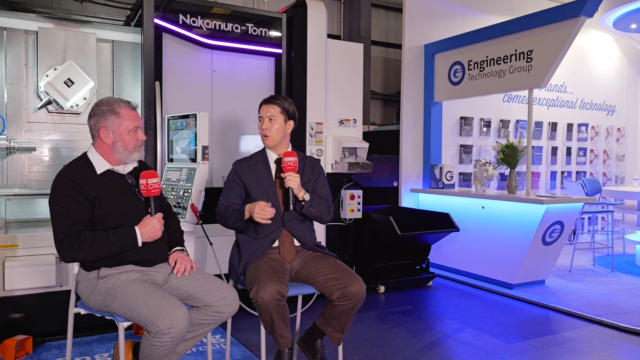
Over twenty-five years of partnership for these global tech leaders
Automation, multitasking, and one-hit machining – that’s where Nakamura-Tome and Engineering Technology group are innovating together…
At the end of 2022, West End Precision Ltd took delivery of its eighteenth Nakamura-Tome turning centre from the Engineering Technology Group (ETG) – a machine that landed only months after Nakamura number seventeen.
The Bideford subcontractor serves the automotive, aerospace and general subcontract manufacturing supply chain; all industries that have faced challenges in recent years – but business is certainly booming now. In 2022, the company took delivery of a Nakamura-Tome NTY3-150, a WT150II and it has just added to the plant list with a Nakamura WT150IIF, the third WT150 series machine in 18 months. With over 15 sliding head lathes, multi-spindle autos, centreless grinding and 18 Nakamura machines, West End Precision is no run-of-the-mill manufacturing business.
As Alex Dziurzynski from West End Precision says: “We are predominantly a high volume manufacturer and we will typically set the machine and run it for a long time. We do all the programming at the console, we don’t do any off-line programming and the onus is that once the machine has been set – it will keep running. This means we can have one operator running multiple machines – and as long as the machines are running and the spindles are turning, we are making money. The Nakamura machines give us that ability.”
The Success
“Our customers went a little quieter a couple of years ago, but since Covid, things have just continued to grow. We are working double shifts and we have added three night shifts just to keep up with demand. Our biggest customer has probably doubled in size and their demand has gone up massively – and we just have to keep up. Hence the level of investment we are putting into the business at the moment. We can’t continue with the equipment that we have got, so we are replacing older machines with much faster new machines.”
Discussing why the North Devon company has purchased the Nakamura-Tome WT150IIF twin spindle twin turret turning centre, Alex adds: “The latest WT150IIF has replaced a Nakamura TW20 that has reliably run for around 20 years. Whilst the new machine is more than 50% faster than its predecessor, it would be unfair to draw direct productivity comparisons.”
However, the benefits of the latest Nakamura are evident, as Alex continues: “The first benefit is that the new machine will just run continuously without any breakdowns. This would sometimes occur on older machines. In a production environment, we need maximum uptime and the Nakamura WT150IIF is running from 8am Monday to 5pm Thursday without stopping. Previously, these parts would require manual input for several reasons. Firstly, there would be tolerance fluctuations with legacy machines and operators would have to intervene to keep production within tight tolerance bands. This issue would be compounded by indifferent tool life monitoring capabilities on old machines where staff would need to regularly check tool life and performance. With the new Nakamura, the alarms and tool life monitoring are exceptional, and we have eradicated excessive tool changes and monitoring protocols. The team know exactly when the tools require changing and this has improved tool life, consistency and machine uptime.”
The new acquisition has been tasked with machining a family of Aluminium 6026 components for a brake system manufacturer. Discussing this, Alex says: “We machine two different parts in batches of 10,000 to 20,000-off with the WT150IIF producing around 6,000 parts a week. The 60mm diameter cast billets were previously machined on a gantry-loaded machine and the major saving has arrived from our ability to change to bar stock and barfeed the parts on the Nakamura WT150IIF – slashing the component loading times.”
Looking at the bigger picture, Alex says: “We have to take a holistic approach to our business. Up to 50% of our Nakamura machines are now over 10 years old and whilst they run very well and reliably, we are investing in the latest Nakamura technology to increase our performance. This performance improvement is arriving via several avenues that we are noticing on the WT150IIF machines. Firstly, our cycle times are falling significantly and we can get more parts out of the door. Moreover, it’s the ability to consistently run long batches without tolerance deviation while minimising operator intervention for tool changes, conformity checks and re-setting. On our night shift, three operators can comfortably manage 10 Nakamura’s and this is not necessarily the case with older machines. The tooling is completely interchangeable with our other latest generation Nakamura’s, and this is enabling us to reduce our set-up times.”
With energy efficiency set to play a key role for manufacturers as they arrive at the end of their fixed rate energy tariffs, Alex adds: “Investing in new equipment may be a large capital outlay, but the productivity, tooling, labour and energy efficiencies will reap rewards and minimise the impact of increasing energy costs. With more than 35 machine tools on-site, our energy costs are considerable and investing in new plant will minimise the impact. Furthermore, we are an environmentally conscious manufacturer and the latest Nakamura WT150IIF has been specified with ETG’s new Amorphous Core Transformer (ACT) technology that will reduce power consumption and CO2 emissions. At present, we are only monitoring power consumption costs for the entire site, but we will measure the performance of the Nakamura WT150IIF with ACT and compare it against existing machines. If the benefit is considerable, we may be investing further in the future.”
Before the energy cost crisis, ETG estimated that an Amorphous Core Transformers would yield an average saving of £25,500 and reduce CO2 emissions by 40,000kg over 10 years on each machine. With some manufacturers witnessing energy cost increases of 100 to 300%+, the potential savings of the Amorphous Core Transformers will certainly be something for businesses to consider.
Taking a look at the Nakamura-Tome brand, in particular, Alex concludes: “The technology continues to move on and this is evident with the latest Nakamura machines. So, Nakamura is stepping forward, we are not standing still and neither is ETG with their machine technology and the Amorphous Core Transformers, which is highlighting their awareness of issues that impact customers. We are certainly on this journey together.”
Be first to see all the updates from MTDCNC
Our newsletters frequency varies dependant on content
All the latest deals from the industry feature on our newsletters