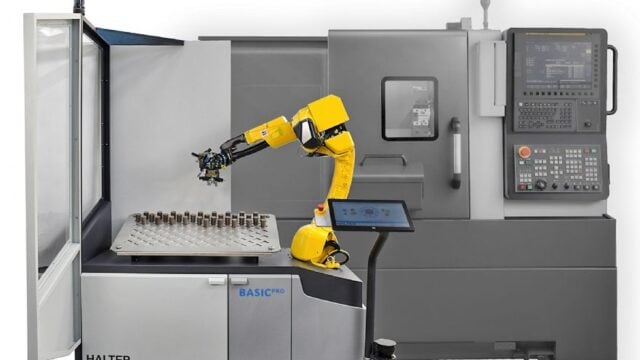
Halter Basic Pro Offers Competitive Entry-Level Automation Solution for Machine Tool Loading
As manufacturers strive to stay competitive in the global market, automatic loading and unloading of machine…
At the Elland, West Yorkshire factory of Archway Engineering (www.archway-engineering.com), which manufactures drilling equipment for site investigation, mineral exploration, water well construction and environmental monitoring, a Leadwell V-50L 3-axis VMC (vertical machining centre) performs some of the more arduous machining operations on the shop floor. Remarkably, the productivity of parts going through this machine has been doubled simply by changing the way workpieces are clamped.
The transformation has been achieved by the purchase in September 2023 of three US-made Chick OneLOKs from sole UK agent 1st Machine Tool Accessories, Salisbury (www.1mta.com). One of the units remains permanently at one end of the machine’s 1,420 x 610 mm table, where it has been clocked into a known position to within 10 µm across the 152 mm face of the clamp’s fixed hard jaw. The other two OneLOKs may be removed to make room to mount a 4th axis indexer, but they are quick to set up again relative to the permanently-positioned clamp by means of a parallel bar.
During frequent small-batch runs, it is a simple matter to secure three parts side by side, write a sub-program to machine the workpiece in the permanent OneLOK, probe the position of the parts in the other two clamps, repeat the sub-program twice at the appropriate offsets, and run the complete cycle in one go.
This process differs markedly from previous practices involving either bulkier conventional vices, only two of which would fit on the table, or a lathe chuck for holding round parts, an arrangement so large that just one could be accommodated in the working area. The positions of all these former workholding setups were slow and laborious to establish accurately and in practice each machining cycle was executed individually.
Another advantage of the Chick product is that it has a time-saving ratchet mechanism to allow the operator to adjust the position of the rear, moveable jaw in one swift action so that it almost touches the workpiece. A few turns of a handle move the jaw in the same direction over the last few millimetres to complete the clamping action quickly, contributing further to short setup times. The mechanism’s novel squeeze clamping action with pull-down as the jaws close applies an equal and opposite force on both sides, resulting in repeatability to within 20 microns.
A practical example of the time savings is in the production of a so-called TC shoe for a drilling machine, produced from an S355 hot-finish steel tube weighing 50 kg. Setting up three billets in machined aluminium jaws side-by-side in the OneLOK takes 1.5 hours, compared with a total of four hours previously needed to clamp the parts individually one after the other in the lathe chuck on the VMC table.
Furthermore, clamping forces were lower using this workholding equipment, as well as when employing conventional vices, compared with up to 26.7 kN of retaining force exerted by a OneLOK. Therefore feed rates previously needed to be slower, lengthening cycle times. The versatility of the new units to hold prismatic parts in hard steel jaws, or round parts in soft aluminium jaws machined to match the shape of the component being secured, sets the Chick product apart from conventional vices and underpins the elevated gripping pressure.
Danielle Toner, production manager at Archway Engineering commented, “Most of our production involves one-offs or small batches, with individual cycles generally running for several hours. Being able to clamp parts of any shape so firmly in the OneLOK allows us to mill much more aggressively using high-feed inserted end mills and solid carbide drills. In one instance, an EN8 steel drive unit end plate that previously took six hours to machine is completed in one hour.”
She explained that it is now possible to feed at 7 m/min a 32 mm diameter end mill rotating at 1,200 rpm, whereas the previous maximum feed rate was 2 to 3 m/min. At the same time, higher quality tools may be employed and depth of cut has increased from 0.3 to1.0 millimetre. Additionally, because parts are held more rigidly and the OneLOK is of low-profile design, there is less vibration so tools last longer and the machined finish is better. It helps particularly with production of the TC shoe as well as phosphor bronze sliding plates, both of which require features with a near-polished surface.
Mrs Toner concluded, “The quicker setup times using the Chick OneLOKs and the faster machining cycles that their secure clamping allows means that a typical short batch of parts can be produced on the Leadwell in two days, compared with up to one week previously.
“I estimate that productivity across the parts produced on this VMC has increased by 100% and probably more. The machine operator is also more productive, as he has extra free time and can plan his work around the factory more effectively. “Overall, our investment in Chick workholding has been a fantastic success and the advice and service provided by 1st Machine Tool Accessories have been first class.”
Stay up to date with the latest industry news and events.
Be first to see all the updates from MTDCNC
Our newsletters frequency varies dependant on content
All the latest deals from the industry feature on our newsletters